In this article, we will comprehensively explain the term surface roughness, and how it affects processing accuracy. Different surface roughness height parameters and common methods used for surface roughness measurement will be elaborated. After that, you will be introduced to the factors affecting the surface roughness of the workpiece, and finally, how to control the surface roughness, will be discussed.
What is Surface Roughness
The measure of the finely spaced micro-irregularities on the surface of the workpiece is termed the surface roughness of the workpiece. The surface of the workpiece will have a smaller pitch, minor peaks, and valleys. In simple words, the inherent irregularities found on the surface of the workpiece as a result of the processing process are called surface roughness. The smaller the degree of the surface roughness, the smoother will be the surface of the workpiece.
The most common parameters used to describe surface roughness are Ra (Arithmetic Average Roughness), Rz (Mean Roughness Depth), Rq (Root-Mean-Square Average Roughness), and Rt (Total Roughness Height). These parameters provide an indication of the level of roughness on a surface, which can affect the performance or function of a material.
For example, it may affect how fluids flow across the surface, how much friction is generated, or how much light is reflected. Surface roughness can also affect the fatigue life of a material, as it can contribute to stress concentrations that cause premature failure. It is important to have an accurate measurement and understanding of surface roughness parameters in order to optimize the performance and life of a material.
Surface Roughness Chart and Its Applications
Surface roughness is used to measure the average deviation of a surface in terms of micrometers or microinches. The lower the number, the smoother and flatter the surface is said to be.

Ra0.4 µm – Shiny, highly polished finish. it’s often used in optical lenses and reflective surfaces.
Ra1.6 µm – A smooth finish with a glossy appearance. It’s commonly used in medical applications as it provides good sealing capabilities and fluid resistance due to its low surface energy.
Ra3.2 µm – This is the standard finish or typical machined finish. It’s used in general engineering and automotive work, as well as many other applications where the surface needs to be slightly more textured than a smooth finish.
Ra6.3 µm – A coarse finish with a satin appearance. It’s often used in auto body parts and industrial components that need improved abrasion resistance or slip resistance.
Ra12.5 µm – A very coarse finish with a dull appearance. It’s commonly used in parts that need increased friction or higher wear resistance, such as drill bits and molds for plastic injection molding.
Ra25 µm – An extremely coarse finish with a rough appearance. It’s often used in parts that need excellent resistance to wear and abrasions, such as mining tools or oil drill bits.
By understanding the surface roughness chart, you can determine the right finish for your specific application. This is especially important in applications where choosing the wrong finish can lead to decreased performance or even failure of the part. Always consult an expert to decide what kind of roughness to use.
Surface roughness is often an important factor when it comes to creating functional items and components. Understanding how different Ra values correspond to different textures helps designers get the most out of their materials and parts. Doing so can help ensure that items will perform as expected without any unwanted surprises or problems.
It is also important to remember that Ra values are just one metric used to measure the surface quality of an item or part. Other factors such as wear resistance, thermal expansion, and corrosion resistance should all be taken into account to get the best results.
How the Surface Roughness Affects Processing Accuracy
Surface roughness plays an important role in determining the surface quality and surface texture of the workpiece. As well as, it also influences the processing accuracy of mechanical processing. In the past, it would have been used for measuring the part’s quality. But as the technology evolved and it revolutionizes CNC machining, the factor of surface roughness has become immensely vital in the product quality determination of the workpiece. The surface roughness affects the fit, wear resistance, the fatigue strength of the workpiece, the friction coefficient of the workpiece pair, its service life, and the overall appearance of the final part.
For high precision and errorless part, its material should not have only excellent (physical, mechanical, and chemical) properties, its machining accuracy should not have only excellent (size, shape, and position) accuracy, and it must not bear the different mechanical process (cutting, grinding, smoothing, etc.) only. But the part necessarily has a qualified surface roughness too.
Generally, the surface roughness is inherent from the particular processing method used and obviously, many other factors contribute. These include the friction generated between the tool and the surface of the workpiece during processing, the plastic deformation of the surface layer metal when the chips are separated, and the high-frequency vibration in the processing system. Due to the difference in processing methods and workpiece materials, the depth, density, shape, and texture of the traces left on the processed surface are different.
Surface roughness is closely related to the matching properties, wear resistance, fatigue strength, contact stiffness, vibration, and noise of mechanical parts, and has a great impact on the service life and reliability of mechanical products.
To avoid potential issues with surface roughness, manufacturers often employ surface finishing techniques to improve the smoothness of the material. Common techniques include sanding, polishing, grinding, and chemical etching. These processes can help reduce the level of roughness on a surface and provide a more consistent finish. In some cases, additional treatments such as plating or anodizing may be necessary to achieve the desired level of smoothness.
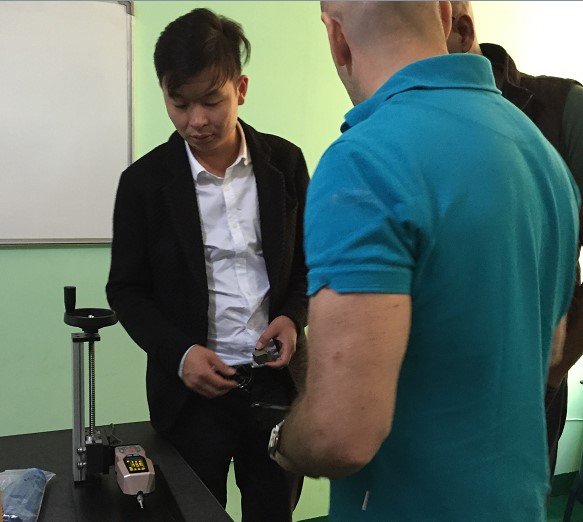
Surface Roughness Height Parameters
Surface roughness is a technical index used to calculate the surface quality of the workpiece. It should not affect the mating properties, wear resistance, corrosion resistance, contact stiffness, fatigue strength, sealing properties and appearance of the parts. Therefore, keeping in view the functional requirements of the parts, it is recommended that the surface roughness of the parts should be clearly mentioned on the drawings.
The prime criterion used to evaluate the surface roughness of the workpiece is Ra and then Rz and Ry. These are defined as follows
Contour Arithmetic Mean Deviation (Ra)
The arithmetic average of the absolute value of the distance between the point on the contour line in the measurement direction (Y direction) and the reference line, within the sampling length is called Contour Arithmetic Mean Deviation (Ra).
Ten-Point Height of Microscopic Unevenness (Rz)
The sum of the average of the 5 maximum profile peak heights and the 5 maximum profile valley depths within the sampling length is called Ten-Point Height of Microscopic Unevenness (Rz).
Maximum Profile Height (Ry)
The distance between the top line of the highest peak and the bottom line of the lowest valley of the profile within the sampling length is called Maximum Profile Height (Ry).
The formula to calculate the value of Ra is given as follows
Ra=1/l ∫t0|Y(x)|dx
Or
Ra= 1/n ∑|Yi| (Approximately)
Where,
Y= Distance from the point on the contour line to the reference line (center line).
∫= Sampling length.
An electric contour instrument is used to measure arithmetic mean deviation and the process is completed by the instrument automatically. The smaller the value of Ra, the smoother will be the surface of the part and vice versa.

Factors Affecting the Surface Roughness of the Workpiece
- Stability of the Machine Tool
The stability of the machine tool is necessary to minimize the surface roughness of the workpiece. For a perfectly stable machine tool, the running accuracy of the main shaft, the stability of the feed system, and lubrication should be maintained. The movement accuracy of these is directly reflected on the surface of the workpiece and in turn, affects the surface roughness of the workpiece.
- The Rigidity of the Workpiece
The rigidity of the workpiece is generally determined from its constitute martial and it mainly refers to the slender and thin-walled workpiece with weak rigidity. Minor Cutting force, temperature, and system vibrations affect this sort of workpiece vibrantly. In turn, the cutting process becomes harder to execute, and cutting vibrations mainly hinder the smooth execution. Ultimately, the surface roughness of the workpiece becomes difficult to achieve.
- Tool Rigidity
Tool rigidity also important for the surface roughness. Tool rigidity depends on the cross-sectional area and the length of the toolbar. To achieve good tool rigidity, the general rule is, the cross-sectional area of the tool should be large, and the length of the toolbar extending from the fixture should be short. But the opposite of this will create difficulties.
A tool having good rigidity means that there will be no self-excited vibrations between the tool and the workpiece. But whenever these vibrations occur, then there will be chattering. When chattering occurs, the cutting force changes right away and result in periodic changes in cutting force and frictional force. Then these vibration lines appear on the surface of the workpiece. These vibrations cause resonance and alternatively, the amplitude will rise. Which generates the noise and when noise generates, then the surface roughness of the workpiece and product quality affect. For good tool rigidity, the rule mentioned above must be applied effectively.

Common Methods Used for Surface Roughness Measurement
Comparative Law
This method is used in the factories frequently but the results using this method are not accurate enough. In this method, vision (eye or magnifying glass) or touch with hands is used. The measured surface is compared with a comparison sample block to measure the surface roughness.
The drawback of using this method is that it does not produce any accurate results and the empirical factors are large. The roughness parameter value can only be calculated up to a rough range.
Stylus Method
In this roughness measurement method, a diamond stylus is used to contact the surface to be measured and slide the stylus gently along it. The tip curvature radius of the diamond stylus used will be about 2 microns. An electrical length sensor is used to convert the up and down displacement of the diamond stylus into an electrical signal. When amplification, filtering, and calculation complete then the display meter shows the value of the degree of surface roughness.
The measuring tool that is used to display the surface roughness value is termed as the surface roughness measuring instrument and the tool that is sued to record the surface profile curve is known as the surface roughness profile meter. These both measuring tools use electronic circuits that can automatically calculate different surface roughness height parameters (i.e., Contour Arithmetic Mean Deviation Ra, Ten-Point Height of Microscopic Unevenness Rz, Maximum Profile Height Ry). The method offers a very good measurement efficiency and is recommended for surface roughness measurement with Ra 0.025~6.3 microns.
Light Section Method
This method surface roughness measurement is based on the light section principle. Whenever the light passes through the slit then a light band is formed and this light band is projected on the surface to be measured. The surface roughness is measured from the profile curve and this curve is formed when the light intersects with the measured surface.
When the light emits from the light source then it passes through the condenser, the slit, and the objective lens. Then the slit is projected to the measured surface at an inclination angle of 45° to form a cross-sectional profile of the measured surface, and then the image is enlarged and projected to reticle. The measurement tool used in this method is called a light section microscope.
This method offers a high measurement accuracy and is suitable for measuring the surface roughness with Rz and Ry values of 0.8-100 micrometers. But not suitable for the measurement of high roughness surfaces and irregular surface measurements.
Interference Method
This method works on the principle of the light wave and measures the surface roughness as interference fringe patterns. A high-magnification microscope is used to enlarge the microscopic part of the surface and the magnification is generally up to 500 times. A tool used for measurement is called an interference microscope. This method is suitable for measuring surfaces with roughness values of Rz and Ry of 0.025 to 0.8 microns.
How to Control the Surface Roughness of the Workpiece
The surface roughness of the workpiece can be reduced using different methods and it is highly recommended that one must have enough understanding, practice and should master them to get the desired results.
1 Selection of Cutting Amount
Cutting amount refers that how intelligently the cutting feed is used. The cutting amount should selected be according to the specific requirements and the material of the part, system temperature, the cooling method used, etc. Cutting amounts can be used to reduce the amount of surface processing of the workpiece.
2 Selection of Tool Geometry Parameters
The selection of the tool geometry parameters should be in such a way that the secondary deflection angle should be reduced and the arc radius of the tooltip must increase. If required, the wiper can be ground which will make the cutting easier and reduce the surface roughness.
3 Controlling the Vibration of the Machine Tool
Vibration contributes a lot to the surface roughness of the workpiece. It can be reduced by applying proper cutting fluid, appropriate coating on the cutting tool, and reducing cutting velocity. Appropriate heat treatment can also be applied to such parts with tough materials.
4 Choosing Raw Material Carefully
The raw material is not only vital for surface roughness but for the whole CNC industry, it is very crucial. It should be selected according to the part’s specifications, cutting speed, processing, etc. The poor selection of raw material will result in poor surface roughness of the workpiece.
Conclusion
Surface roughness is an important factor to consider when designing components and products. Different Ra values correspond to different textures, which can affect the performance of a component or part. By understanding the surface roughness chart and consulting with experts, designers can ensure that items will perform as expected without any unexpected issues or failures. With the right knowledge and advice, designers can have confidence that their components will achieve the desired level of performance.