Computer has become a part of every machine nowadays. From a small blender machine to large distributed control systems, every machine is now operated using different control techniques. Without doubt, technological advancements have made contributions in every field of engineering.
History of CNC machining date back to 1952 when Richard Kegg, in collaboration with MIT, developed the first CNC milling machine named as ‘’Cincinnati Milacron Hydrotel’’. Five years later, in 1958, he filed a patent for a “Motor Controlled Apparatus for Positioning Machine Tool”. This was the commercial birth of automated machining technology.
What is CNC machining?
CNC machining is a term commonly used in manufacturing and industrial applications, but exactly what does the acronym CNC stand for and what is a CNC machine?
The term CNC stands for ‘computer numerical control’, and CNC machining is defined as a subtractive manufacturing process which typically employs computerized controls and machine tools to remove layers of material from a stock piece—known as the blank or workpiece—and produces a custom-designed part. This process is suitable for a wide range of materials, including metals, plastics, wood, glass, foam, and composites, and finds application in a variety of industries, like Communications, Machines Fabrication and Aerospace parts. When speaking in terms of the machine itself, the CNC machine definition is that it represents the actual programmable machine that is capable of autonomously performing the operations of CNC machining.
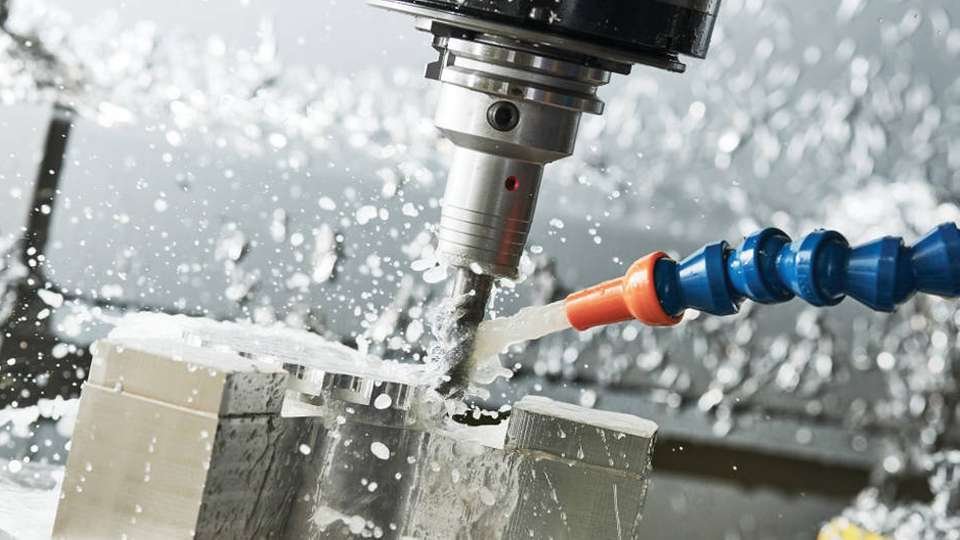
Subtractive manufacturing processes, such as CNC machining, are often presented in contrast to additive manufacturing processes, such as 3D printing, or formative manufacturing processes, such as injection molding. While subtractive processes remove layers of material from the workpiece to produce custom shapes and designs, additive processes assemble layers of material to produce the desired form and formative processes deform and displace stock material into the desired shape.
The automated nature of CNC machining enables the production of high precision and high accuracy, simple parts and cost-effectiveness when fulfilling one-off and medium-volume production runs. However, while CNC machining demonstrates certain advantages over other manufacturing processes, the degree of complexity and intricacy attainable for part design and the cost-effectiveness of producing complex parts is limited.
The workpiece material and its physical properties are used to determine the optimal cutting speed, cutting feed rate, and depth of cut. Measured in surface feet per minute, the cutting speed refers to how fast the machine tool cuts into or removes material from the workpiece. The feed rate—measured in inches per minute—is a measure of how fast the workpiece is fed towards the machine tool, and the cut depth is how deep the cutting tool cuts into the workpiece.
Typically, the workpiece will first undergo an initial phase in which it is roughly machined to the approximate, custom-designed shape and dimensions, and then undertake a finishing phase in which it experiences slower feed rates and shallower cut depths to achieve its more precise and accurate specifications.
What are Benefits of CNC machining?
In recent years, CNC machining has been steadily overtaking the traditional machining industry. Thus, the recent shift of major manufacturing companies to utilize the power of CNC machining over convention methods does not come as a surprise. Industries like healthcare, military, and aerospace need precision parts with tolerances as tight as +/- .0005, which is very difficult to achieve with conventional machining.
With increased accuracy and reduced cost and time, machining processes using computer numerical control techniques have a lot of benefits over traditional machining processes in production. Here I’ve listed down a few major advantages which are beneficial for customers as well as vendors.
Accuracy in measurements:
The manufacturing market relies heavily on computer-numerical control (CNC) machining, including operations that once used engineer-operated equipment like routers, shaping machines, vertical millers, and center lathes. In all these cases, the labor force is reduced, and accuracy is achieved.
Due to accurate results in machining, manufacturers from all over the world prefer CNC machining for their required fabrication. Industries like aerospace, automotive, agriculture, construction, electronics, firefighting, manufacturing, metalwork, military, and chemical handling will need accurate, complex, and consistent cuts.
CNC machines eliminate chances of human error and help in achieving accuracy within 1/1000th because the use of a CNC almost eliminates human error, CNC machines are highly consistent and accurate, providing clients with uniform and faultless products. This is what makes CNC machining so crucial for areas where quality is critical, as the level of reliability and quality in the work produced is much higher.
Ideal for creating batch production:
CNC machining provides an efficient, expedient, and precise production capacity ideal for creating large quantities of mechanical and plastic parts.
It is as easy as someone is using a photocopy machine or print machine. You give a single command to the machine and then it prepares a whole batch of paper according to the given command. Similarly, workpieces are prepared in batches with a single command. Whereas in traditional machining, the operator must give slow equal feed in every single pass on every single job piece. Consequently, it will reduce labor force requirements and increase mass production in less time.
Less labor is very beneficial in terms of cost-effectiveness and business management. Invest a single time in a CNC machine and it will save cost in every single workpiece produced. Every piece has the same length, width, height, and diameter in CNC machining which makes exact copies of the prototype.
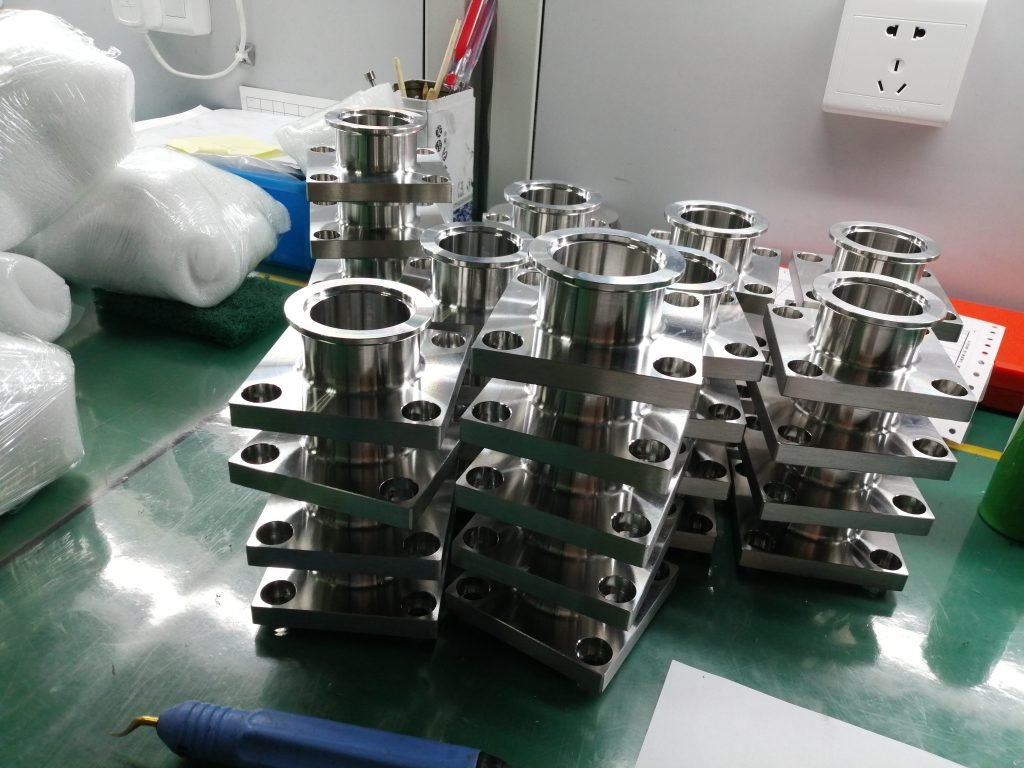
High-speed production rate:
Since every operation is performed automatically and precisely, it eliminates much of the time-consuming trial and error associated with manual machining processes. CNC machines can work for hours without any assistance, only programming is required once then it continues its execution for hours in huge quantities.
Less tool arrangement:
In traditional machining, a workpiece will be done by more tools like cutting, drilling, boring, taper turning, and facing, whereas less tools are required in CNC machining.
Using conventional machining, you become always dependent on the required labor force and if they are on leave or get sick, your machine is useless, just lying there doing nothing. Shot staffing does not affect directly to CNC machining because it already requires one to two persons for work. So, a single person can manage the work on two machines if required.
Ability to produce intricate designs
CNC machines are capable of producing more intricate designs with greater accuracy than manual machines. They also require less maintenance and are more reliable, meaning that there is less risk of human error. As a result, CNC machining can provide tremendous savings in time and cost over traditional methods.

Cost-effective:
CNC machines use higher levels of automation and reduce possible errors while increasing productivity and cost-effectiveness across the board. Also, CNC machines can be reprogrammed in a short period of time to produce a completely new product, making them ideal for short or long production runs. You can change programming without being time-consuming or too costly.
More Capability:
CNC machines can create such complex parts that can not be replicated by conventional machines. These machines can produce different shapes, sizes, and textures using a 3-dimensional tools adjustment. CNC machines have a lot of capabilities like design retention, codded programs can be easily applied to every single piece regardless of external factors such as changing machine operators.
Many complex and intricate operations can be performed using CNC machining.
CNC machines more than makeup for their initial costs with a high rate of output and a lower number of mistakes in resulting components. Operators also require less training to operate a CNC machine and can learn how to use the machine in a virtual environment, eliminating the need for training workpieces. As these machines become more popular and widespread, their cost will continue to drop.
Better Safety:
There is no chance of an accident in CNC machining because the machine is fully covered by the casing and no direct human involvement is required. While traditional machines require direct human involvement, workers can get injuries, especially on fingers because tools used in lathes, drills, punches, and other machines are very sharp.
Any hazardous safety issues, such as a jam or other machining error, are only detrimental to the machine and not a safety issue for the operator, unlike conventional open guard machining.
Conclusion
Overall, CNC machines offer greater accuracy, speed, and efficiency than traditional manual machining methods. They are capable of producing complex shapes with better precision that can’t be achieved with manual machines. They are also less labor-intensive, require less maintenance, and can store multiple programs for faster production. As a result, CNC machining is an ideal solution for large-scale production runs or high-precision components that require intricate designs.