What is CNC Brass?
CNC brass is a process of machining brass using computer numerical control (CNC) technology.
CNC brass machining is a precise and efficient way to create high-quality brass parts, it can be used to create a wide variety of parts, including everything from jewelry to plumbing fixtures and automotive parts. This process is often used when traditional machining methods would be too time-consuming or expensive.
Brass Parts Manufacturer
Brass parts are often used in machining applications because of their durability and resistance to wear. At Shanghai Elue, we specialize in brass machining and we can use state-of-the-art equipment and a team of experienced machinists to produce high-quality brass parts.
We offer brass machining services for a variety of industries and can provide both small and large production runs.
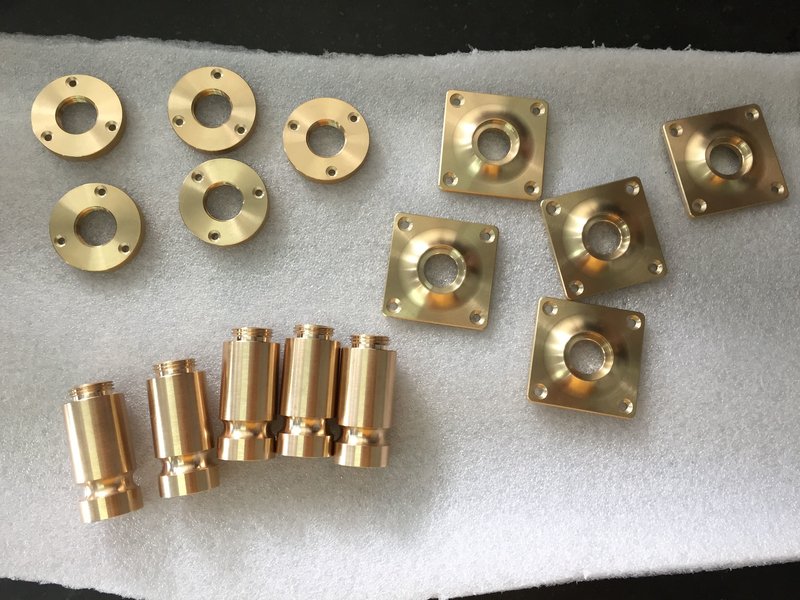
Types Of Brass Grades For CNC Machining
There are three main brass grades that are typically used for brass machining: C360, C380, and C260. Each brass grade has its own set of properties that make it ideal for different applications.
C360 brass is the most popular brass grade for machining. It has excellent machinability and is easy to form and weld. This brass grade is often used for general-purpose applications such as plumbing and electrical fittings.
Besides, this brass grade has excellent cold working properties and is easily soldered and brazed.


C260 brass is a leaded brass that is easy to machine and has good corrosion resistance. This brass grade is often used for electrical fittings, musical instruments and other applications where a high degree of malleability is required. This brass grade is easy to machine and can be easily formed into complex shapes.
C260 brass is also known as “cartridge brass” because it is often used for making ammunition cartridges.
C380 brass is a high-strength brass that is often used for applications that require high strength and durability, such as plumbing fittings and electrical connectors.. This brass grade is more difficult to machine than C360 brass but can be heat treated to increase its strength.
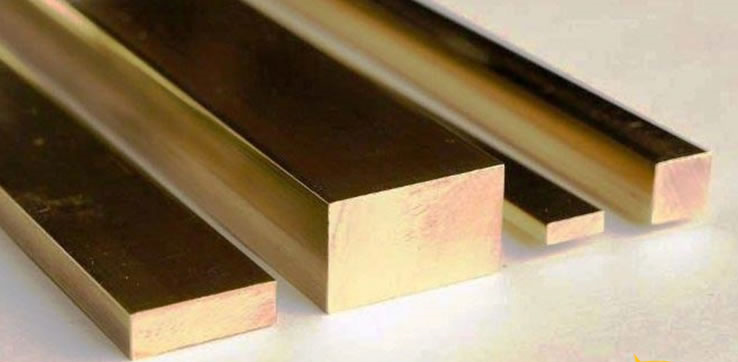
What Are the Advantages of Brass CNC Machining?
Brass is a popular choice for CNC machining, and brass machining offers many advantages over other methods of fabrication. The main advantages of brass CNC machining are:
– Low friction coefficient. This makes it ideal for use in bearings and gears.
– Easy to be machined. Brass alloys have better machinability than many other metals, which makes them popular for machining.
– Resistance to corrosion. This feature makes it an ideal material for applications where longevity and reliability are important.
– Excellent electrical conductivity properties. Brass is suitable for use in electrical components and circuits.
– Superior strength and durability. This metal is often used in the production of musical instruments, plumbing fixtures and electrical components.
Brass Surface Finishing Options
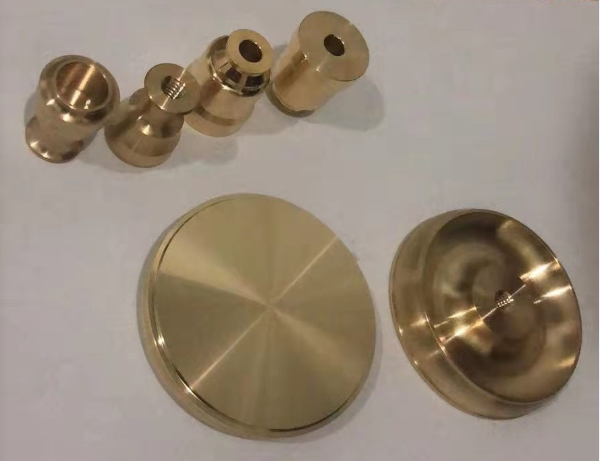
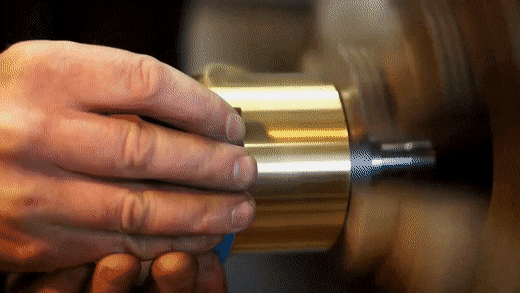
- Chrome Plating or Nickel Plating: Brass is often plated with harder metals such as chrome or nickel to extend its wear resistance. Plating brass with these materials also provides a more appealing aesthetic finish.
- As Machined: In most cases, brass machined surface is good-looking and you don’t need any additional finishes.
- Hand Polishing: This is the most traditional method of brass finishing, and involves using a variety of polishing compounds and pads to achieve the desired results.
- Honing – Honing is a process that uses abrasive stones to remove small imperfections from the surface of brass.
- Buffing – Buffing is a process that uses a rotating wheel covered in an abrasive material to remove surface imperfections and create a high-gloss finish.
Brass Machining Tips
Working with the correct cutting tools, lubricant, correct feed and speed, spindle liners and also right programming can ensure successful brass machining.
– Use high-speed steel (HSS) tools. This type of tool is designed to withstand the high temperatures that are generated when machining brass. Standard carbon steel tools will quickly lose their edge when used on brass, so it is important to use HSS tools to avoid having to constantly stop and sharpen your tools.
– Use a lubricant when machining brass. A good lubricant will help to keep the brass from work-hardening, and will also help to cool the tools and workpiece, preventing tool damage.
– Use the correct feed and speed when machining brass. The feed rate should be slow enough so that the cutting tools do not overheat, but fast enough to prevent the brass from work-hardening. The speed should be high enough to prevent the tool from binding in the workpiece, but low enough to prevent the tool from breaking.
– Spindle liners, or spindle sleeves, are also important when machining brass. Spindle liners help to protect the spindle from damage that can be caused by the chips and debris that are generated when machining.
– Programming is also important when machining brass. It is important to use a tool path that minimizes the amount of time that the cutting tools are in contact with the brass. This will help to reduce wear on the tools, and will also help to prevent the workpiece from becoming work-hardened.