As the world becomes increasingly more complex, manufacturers are searching for ways to create products that are both innovative and aesthetically pleasing. One way to achieve this goal is through the use of clear plastic injection molding. This process creates parts that are both durable and transparent, making them perfect for a wide variety of applications. Here is some more information about how this process works and why it is such a valuable tool for manufacturers.
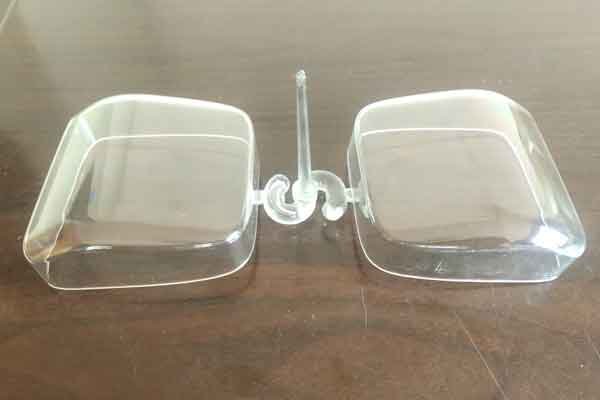
What are clear plastic injection molding parts?
The clear plastic injection molding process is used to create plastic molding products that need to be made from translucent plastic, they have become a popular choice among many industries, like consumer electronics, medical devices, automotive products, and toys. They are also increasingly popular for packaging items like food containers and cosmetic jars. The clarity of these parts makes them ideal for showcasing product designs or providing visibility into the functionality of certain components. In addition, clear plastics can be modified with various additives to increase their durability or impart other desired characteristics such as fire resistance or anti-static properties. Ultimately, the uses for clear plastic injection molding parts are virtually limitless. Whether you’re looking for components in consumer electronics or packaging solutions, clear plastics offer the perfect combination of value and functionality. By understanding what they are and how they can be used, you can ensure that your project will benefit from the advantages of this versatile material.
The process of creating plastic molding parts is relatively simple and involves injecting molten plastic into a pre-made mold, where it cools and solidifies to create the desired shape. Different types of plastics can be used for this process, each with its own benefits, depending on the application. With the right materials and design, clear plastic injection molded parts are an excellent choice for any project.
Most common transparent-plastics features:
# Good chemical resistance.
# Ease of coloring
# The most excellent optical properties with great transparency and gloss.
# The highest climate resistance and surface hardness among plastic materials.
# Common purpose review with great ease and suitable for large shaping or thin wall molding
Advantages of using clear plastic injection molded parts
Clear plastic injection molded parts offer many advantages over traditional manufacturing techniques, including:
• High strength-to-weight ratio – Clear plastics are much stronger than their weight would suggest. For example, acrylics and polycarbonates can be up to 10 times stronger than glass, making them ideal for a variety of applications.
• Cost efficiency – The injection molding process allows for the cost-effective production of large quantities of parts with minimal waste material. This makes it the ideal option when low costs and high volume are essential.
• Consistent performance – Injection molding creates consistent parts that are identical in size and shape, providing reliable performance from part to part.
• Complex designs – Clear plastics are easily molded into complex shapes and can accommodate intricate details, making them perfect for a wide range of applications.
• Durability – With the right materials, clear plastic injection molding parts can be extremely durable and resistant to environmental factors like moisture, UV rays, and temperature fluctuations.
• Versatility – In addition to the many uses above, clear plastics can also be used in a variety of ways including lids, tanks, containers, lenses, windows and much more.
By leveraging the advantages of this versatile manufacturing process, you can make sure your project gets the most out of clear plastic injection molding parts. Whether you’re looking for components in consumer electronics or packaging solutions – these parts offer the perfect combination of value and functionality.
Types of plastics that can be used for clear plastic injection molded parts
The most common types of plastics used for clear plastic injection molding are polycarbonate, acrylic (PMMA), PP and polystyrene.
Acrylic (PMMA)
Acrylic is non-toxic, scratch-proof, and UV-resistant, making it a popular choice for use in outdoor equipment. It has good transparency and is highly resistant to chemicals, making it an ideal choice for applications where visibility is important.
Polycarbonate (PC)
Polycarbonate is strong and impact-resistant, making it suitable for use in protective eyewear or automotive components. Injection-molded polycarbonate can be crystal clear or have a range of colors, and is known for its excellent impact resistance. It’s also used in applications where transparency, aesthetics, and long life are important. Polycarbonates offer excellent strength, impact resistance, and clarity, making them ideal for a variety of applications.
Polypropylene (PP)
Polypropylene is a lightweight material that can be easily molded into complex shapes with thin walls. It’s durable and resistant to a variety of chemicals, temperatures, and solvents. Polypropylene is Commonly used in the medical, automotive and food industries due to its versatility and ability to resist moisture, heat and chemicals.
Polystyrene (PS)
Polystyrene is an inexpensive, lightweight plastic that can be easily injection molded into complex shapes. It has good clarity and excellent stiffness, making it the ideal choice for applications where visibility is important, such as medical equipment and lighting fixtures. PS offers superior clarity as well as excellent electrical properties like insulation and arc resistance. Its low viscosity makes it easy to extrude into thin components without compromising its toughness or strength.
By understanding the advantages of clear plastic injection molding parts, you can make sure your project takes full advantage of this versatile manufacturing process. With a wide range of materials available to choose from, you’ll have no trouble finding the perfect combination of value and functionality for your application. This guide should help you understand the basics of clear plastic injection molding parts so that you can make an informed decision when selecting the best material.
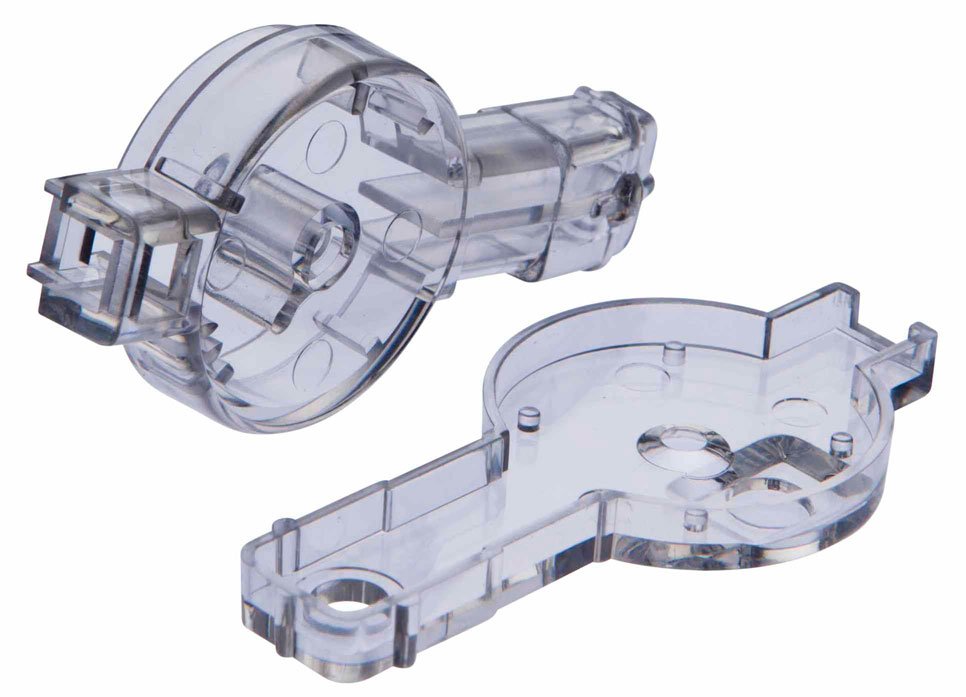
Common problems with clear plastic injection molding process
Clear plasitc molding process has got many benefits, but it is also prone to some common problems. Here I will explain some of them and provide tips on how to prevent them properly. Common problems with the transparent clear plastic injection molding process include dents, warpage, and vacuum voids.
• Warpage is caused by uneven cooling of the molten plastic, this occurs when parts have uneven thicknesses or are not properly cooled. It can cause parts to deform and lead to improper fitment of other components.
• Shrinkage – When plastic cools, it tends to contract slightly, leading to a decrease in size. If the part is too small for its intended application, it could lead to functional issues with the end product.
• Dents are caused by shrinkage of the molten plastic as it cools and solidifies, resulting in a depressed part surface.
• Vacuum voids are the ones formed within the parts due to incomplete filling of the mold cavity. the most common causes of voids include poor material flow, inadequate injection pressure, and insufficient filler pressure.
• Resin selection – Selecting the right resin is essential for ensuring that parts possess optimal properties such as clarity, strength and flexibility. Poor material selection can lead to costly rework or scrap materials.
To avoid these sorts of major issues, the material temperature of the molten plastic must be carefully controlled so that the raw material is evenly distributed all through the shape depth. In addition, proper packing pressure must be used to ensure that the molten plastic fills the mold cavity.
Below let’s discuss the preparation and drying of raw materials and screw, barrel, and accessories cleaning:
# Preparation and drying of raw materials:
Since any small impurity in the plastic may affect the transparency of the product, and therefore storage, filling process and transportation must pay attention to sealing, to ensure that the raw materials are clean. In particular, the raw material contains moisture, which will affect the raw material to deteriorate after heating, In this injection molding process, the material must be included using a dry hopper. In addition, the material must be stored and mixed according to the supplier’s instructions.
# Screw, barrel and accessories clean:
The screw is part of the molding machine that serves as a means of transferring heat into the plastic melt in order to prepare it for injection. The most common problem with injection-molded parts is contamination due to build up on the screw or barrel walls. To prevent this from happening it is important to regularly inspect and clean these components. In addition, any rubber o-rings or seals should be replaced when they start to wear out as these can also cause contamination issues. Proper cleaning and maintenance of these components will help ensure high quality clear molded parts every time.
The defects of transparent plastic parts molding and its proper solutions
Proper care should be taken during the processing of clear plastic moulding. It’s more complex compared with other colored parts. Some different clear plastic moulding parts include PC, PMMC, POM, ABS, and PET. These clear plastic kits are used widely in cosmetic packaging, water tank, medical devices, food packs, auto lights, and car parts.
Silver streak:
This is common during the filling and cooling process due to expansion that will weaken the plastic parts. Annealing is one of the solutions since plastics in PC materials can be heated and allowed to cool naturally. This strategy can eliminate the silver streak which occurs due to wet resin. However, it is crucial to ensure the resin is dry before proper processing.
Air bubble:
During the clear plastic molding process, the air and water in the resin can get trapped inside the cavity due to excessive cooling and insufficient filling, leading to a vacuum bubble. This problem can be solved by:
# Drying up the transparent plastic raw material before pouring them into the barrel. This may significantly reduce water contained and air.
# Slow down the filling process and give more time to allow air escape.
Surface scratch:
The processing and cooling condition may also be improper which can result in visible surface scratches. This issue can typically be resolved by using a better material with higher hardness. Moreover, the design of plastic part should also be taken into consideration to reduce friction when releasing the plastic parts from the mould.
Surface gloss defects:
This is another common issue with clear plastic molding. It happens when the shape surface is not well polished or cooled down too fast. This prevents the resin from getting into a molded state. To resolve this problem, the molding normal temperature and ejection pressure should be increased. The cooling time ought to also final longer.
Vibration pattern:
It refers to the dense corrugation formed from the sprue as the same center. The reason is that the melt viscosity is too big, the front conclusion material has been condensed within the cavity, and then the material breaks through this condensation surface, and Vibration lines show up on the surface.
Finally, it is important to properly train operators for this specific process in order to prevent any defects or mistakes during production.
Mold design tips for clear plastic molding
Designing a part for clear plastic injection molding requires careful consideration of various factors. It is important to accurately design the part for the injection molding process, as any mistakes in this area can cause problems during production. The following tips provide guidance on how to best design parts for this type of molding:
1. Start with a CAD File: Starting from scratch with a CAD file will allow you to create an accurate and detailed digital representation of the part before it goes into production. This will help ensure that no details are overlooked and the resulting parts meet all requirements.
2. Use Clear Resin Materials: Using clear resin materials such as polycarbonate or acrylic provides excellent clarity and is ideal for molded parts requiring transparency.
3. Consider Wall Thickness: It is important to take wall thickness into account when designing the part, as walls that are too thin or thick can cause problems with the injection molding process. Change in wall thickness should be avoided during clear plastic injection molding. If uniform wall thickness is not possible, then make sure that the thinnest part of the part is designed to have more than minimal wall thickness which will ensure product strength and clarity.
4. Avoid Sharp Corners and Edges: Sharp corners and edges should be avoided in designs, as they can cause stress concentrations which leads to cracking or other defects. Creating parts with gentle curves and rounded edges helps to minimize these issues. Chamfer angle should be greater than 45 degrees while corner radius should be at least 0.25mm for achieving smooth surface on the molded parts. This will also help in reducing stress concentration points at corners and cracks due to shrinkage.
5. Optimize Gate Placement: The gate location is an important factor to consider when designing a part for clear plastic injection molding, as this is where the resin enters the mold cavity and affects how it flows through the tool. Identifying an optimized gate placement helps improve the molding process, resulting in a higher quality part.
6. Make certain that the mold surface is smooth: A smooth surface finish is necessary for clear plastic molds in order to achieve a satisfactory result. If there are any defects or irregularities on the surface, they can affect the clarity of the molded part. It’s also important to design cavities with appropriate depth and volume so as to avoid thinning.
7. Transition Slowly from Thick to Thin Areas in Molding: When designing a mold, it is imperative to ensure smooth transition from thick areas to thin areas. This will help in avoiding stress concentration and promote uniform cooling during the injection process.
8. Be Cautious with C-Shaped Molded Parts: C-shaped parts are not recommended for clear plastic injection molding since they can cause optical distortions in the resulting products. If such parts need to be molded, then their design should be changed to a more uniform shape.
9. Consider Conformal Cooling Channels: Conformal cooling channels should be considered since they can lead to a reduction in cycle time, improved quality and better surface finish of the molded part. Properly placed cooling channels can also improve the strength and dimensional accuracy of the part.
10. Avoid Eliminate Undercuts in Molded Parts: Undercuts should be avoided in molded parts since they can cause issues with part ejection and will also produce poor surface finish. If undercuts are unavoidable, then a collapsible core should be used to achieve better results.
Finally, working with experienced professionals in this field will ensure that your project is handled properly and meets all requirements. Whether you are looking for advice on the design phase or need detailed guidance throughout the entire process, an experienced partner can provide invaluable assistance in helping your clear plastic injection molding project succeed.
Conclusion
Clear plastic injection molding is a great option for product manufacturers looking to make highly detailed parts with excellent clarity. However, due to the complexity of this process, it is important to familiarize yourself with common issues that might arise and how to prevent them properly. By following these tips you should be able to design parts for clear plastic injection molding that are easy to produce and result in high-quality molded parts every time.