The food processing industry is a critical part of the modern economy, so the equipment used in food processing plants is essential to ensuring that the food we eat is safe and meets all regulatory requirements. Right now, this industry is increasingly turning to Computer Numerical Control (CNC) machining for various applications, from cutting and shaping metal parts to food packaging. CNC machining has revolutionized the process of manufacturing food products, providing greater accuracy and precision, as well as cost savings. In this article, we will discuss how CNC machining is used in the food processing industry and some of the benefits it offers.

What is CNC machining and How Does it Work
CNC machining is a form of computer-aided manufacturing for creating parts and components for various industries, including food processing. In CNC machining, machines are programmed to move tools in specific directions at certain speeds, following a predefined set of instructions. This enables the machine to create complex shapes and patterns quickly and accurately.
Benefits for Food Processing Equipment Manufacturers
CNC machining offers several benefits for food processing equipment manufacturers, including improved accuracy and precision, faster manufacturing times, and cost savings. CNC machining allows for more precise geometry of parts, resulting in higher-quality products with fewer defects. Additionally, CNC machining is much faster than traditional methods of cutting and shaping metal parts for food packaging, allowing for significantly shorter production times. Finally, CNC machining can save costs for food processing equipment manufacturers due to its high levels of automation and the reduction in waste that it provides.
Accuracy and Precision
The most significant benefit of using CNC machining in the food processing industry is its accuracy and precision. CNC machines are programmed with a specific set of instructions that enable them to accurately cut complex shapes out of hard materials such as steel or aluminum. This level of precision enables manufacturers to produce high-quality parts that meet their exact specifications. Additionally, because these machines can operate at extremely high speeds, they can quickly produce large quantities of parts in a short amount of time. This reduces production times significantly while still ensuring quality control standards are met.
Cost Savings
Another benefit offered by CNC machines is cost-effectiveness. These machines are able to quickly and precisely manufacture parts at an affordable rate, saving both time and money compared to traditional methods used in the past. Additionally, because these machines have a long life span, they can be used for many years without needing any major repairs or maintenance work done on them. This further contributes to cost savings over time since there are no expensive repairs or replacements required down the line.
Ease of Use
Finally, one of the primary advantages that come with using CNC machines is their ease of use for operators in the food processing industry. Unlike manual tools and processes which require more skill and experience from those operating them, CNC machines require minimal training for operators since they are automated systems that need only basic programming knowledge from their users. Additionally, because they can be programmed with specific instructions ahead of time, they provide more consistent results than manual methods which require more trial and error in order to achieve desired outcomes.
In conclusion, CNC machining offers numerous benefits for use in the food processing industry including accuracy and precision; cost savings; ease-of-use; and improved consistency overall when compared to manual methods traditionally used before their emergence on the scene. If you’re looking into ways to improve efficiency while maintaining quality control standards within your business’s operations then you should definitely consider investing in some form of computer numerical control machinery today! With its numerous advantages over traditional methods currently being utilized by manufacturers across all industries today – it’s easy to see why so many businesses have already made this switch!
Applications for CNC Machining in the Food Processing Industry
CNC machining has a wide range of applications in the food processing industry, from cutting and shaping metal parts for food packaging to creating complex shapes for food processing equipment. CNC machining can also be used for engraving text or images onto product packaging for branding and marketing purposes, as well as for the fabrication of custom-shaped molds for casting and forming components for products such as snack foods.
There are a variety of CNC machines that can be used for food processing applications, each with its own advantages for specific tasks. Common types of CNC machines include milling machines, lathes, routers, and grinders. Milling machines create shapes and components by cutting away material from the workpiece with a rotating tool or cutter; lathes use turning tools to shape objects like bowls and spindles; routers carve out intricate patterns in materials such as wood and plastic; while grinders remove small amounts of material for precision finishing on workpieces. Depending on the specific needs of your business’s application, different types of CNC machines may be more suitable for certain tasks than others.
In addition to these common machines, there are also specialty CNC machines for food processing applications. These include machines for forming and shaping doughs for baked goods as well as for cutting, slicing, or deboning meats for further processing. Whatever the needs of your business may be, you can find the right CNC machine for the job. The high-quality materials we use for our components include:


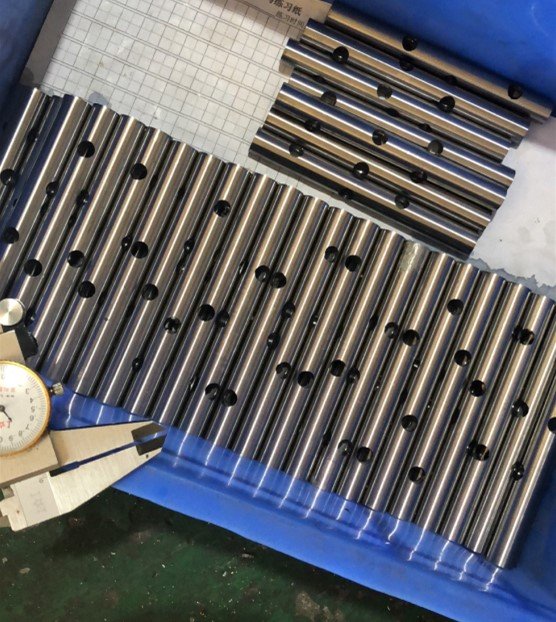
Overall, CNC machining is becoming an increasingly popular choice for the manufacturing of food processing equipment due to its accuracy, speed, cost savings, and automation. By leveraging this technology, food processing equipment manufacturers can ensure that their products meet all requirements and are produced quickly and efficiently.
Typical Food Machine Parts associated with CNC Machining
Shafts: Used for rotary motion in food processing machines, shafts are typically made of stainless steel for corrosion resistance.
Motors: High-quality motors for increased efficiency and minimal noise for food processing machines.
Gears: For transmission and distribution of power between moving parts. Custom-made for specific applications, gears are used to control speed and torque for smooth operation. Gears come in different sizes for various speed ratios needed for different types of food equipment.
Guides: Used for accurate positioning of components in automated processes for greater precision and accuracy.
Poppets: Made from tough materials such as aluminum or stainless steel for a secure fitment into machines.
Rollers: For maximum friction reduction while transferring products through the production line with minimal wear and tear on parts.
Valves: Specifically designed for controlling the flow of liquids or gases through the system. Valves are manufactured from a variety of materials such as brass, bronze, stainless steel, or plastic depending on their application.
Piping: To transfer fluids around the food machine, piping is usually made from stainless steel for durability and flexibility to fit into tight spaces.
Bearings: Designed for high loads, bearings are used for rotary motion and for supporting the weight of moving parts in food machines.
Sensors: Used for the detection of temperatures, pressures, and flow rates for food products. Sensors come in various sizes for easy installation into tight spaces.
Hydraulic Components: CNC machining is used for the precision manufacturing of high-pressure hydraulic components for industrial food machines.
Gaskets: Sealing components for preventing fluid from leaking out of the machine during operation. Gaskets are typically made from rubber or silicone for durability and flexibility.
Conclusion
CNC machining is a valuable tool for food processing equipment manufacturers, and the use of CNC machining for food processing applications is sure to grow in the coming years, as manufacturers continue to take advantage of its many benefits such as accuracy, speed, cost savings, and automation. In particular, automated processes for cutting and shaping doughs for baked goods will be increasingly used for mass production runs for larger businesses. Additionally, new technologies for CNC machining are being developed every day, which will further improve the efficiency and accuracy of food production processes. With its wide range of machines for different applications and new technologies on the rise, CNC machining is sure to continue to be an important part of the food processing industry for years to come.