CNC machining tolerances are critical for ensuring that any given part is produced to the exact specifications required. Incorrectly designed parts or those with inaccurate dimensions can lead to a number of problems later on, such as poor fitment or compatibility issues.
Additionally, CNC machined parts need to be consistent in order to produce reliable and repeatable results. In general, these tighter tolerance requirements lead to higher precision parts, which can often be more expensive when compared to parts made using other manufacturing processes.
In order to produce high-quality parts, it is important to understand and utilize the correct tolerances for the job at hand.
What are CNC Machining Tolerances
CNC Machining Tolerances are the specifications used to describe the acceptable dimensions of a machined part. These tolerances provide guidance on how accurately a machine can manufacture components, and should be considered in the design process. The tolerances define what is acceptable in terms of dimensional variation from the nominal size as well as surface finish and other quality requirements. The more accurate the tolerance specified, the greater the cost and time required to produce the component. It is important to ensure that tolerances are adequately defined in order to meet design requirements while managing cost and time constraints.
4 Types of CNC Machining Tolerances
Three basic tolerances that occur most often on working drawings are limit dimensions, unilateral, bilateral tolerances, and Geometric Dimensioning and Tolerancing.
Limit dimensions are the most common type of tolerance and can be used for parts with simple geometries. These limits define the maximum and minimum sizes of a part’s features that can be machined within acceptable quality levels.
Unilateral tolerances allow for variations only in one direction, either over or under the nominal dimension. This type of tolerance is often used to control the fit of parts when tight tolerances are not required.
Bilateral tolerances allow for variations in both directions, over and under the nominal dimension. These are used in applications where tight dimensional accuracy is needed.

Geometric Dimensioning and Tolerancing:
In addition to the three basic tolerances, geometric dimensioning and tolerancing (GD&T) is used more often for parts with complex geometries. GD&T is a system of symbols that define how a part must be oriented in space. It allows for variations in the form and location of features, enabling tight accuracy requirements to be met.
Below are some commonly used ones:
Flatness: This symbol is used to control the flatness of an area.
Parallelism: This symbol is used to ensure that two surfaces are parallel to each other within a certain tolerance. When it comes to machining tolerances, the parallelism and perpendicularity of components is also important. This determines how well two surfaces will fit together when assembled and must be considered in order to ensure that parts can be properly finished.
Perpendicularity: This symbol is used to ensure that two surfaces are perpendicular to each other within a certain tolerance.
Circularity: This symbol is used to control the roundness of a hole or shaft.
Cylindricity: This symbol is used to control the straightness and roundness of a hole or shaft.
It is important to use the most appropriate tolerances for each machined feature in order to ensure that all parts are manufactured within acceptable quality levels.
Concentricity: This symbol is used to ensure that two circles are concentric within a certain tolerance.

By understanding these various types of CNC machining tolerances, engineers and designers can ensure that the parts they design are machined to meet their expectations. This will help them to produce quality components more efficiently by avoiding costly mistakes due to improper tolerances.
Common Tolerances on CNC Machining
Generally speaking, standard machining tolerances are typically +/- .005” for metal parts and +/- .010” for plastic parts, but these are not absolute and can vary depending on the application. For high-precision parts, +/- .001″ or even tighter is sometimes specified.
Although higher precision can be achieved with more expensive equipment and more skilled machinists, you still need to give a reasonable tolerance to meet your requirement to lower cost. The level of tolerance should be chosen based on the design requirements, cost constraints, and the required quality level of the part.
At Shanghai Elue, the typical tolerances in inches we received from USA customers are often listed below:
one place decimal: +-0.1
two place decimal: +-0.03
three place decimal: +-0.005
By understanding the types and common tolerances of CNC machining, engineers and designers can ensure that their parts are produced to meet their expectations in terms of dimensional accuracy and surface finish. This will help them to produce quality components more efficiently while avoiding costly mistakes due to improper tolerances.
Tips on Choosing Right CNC Machining Tolerances
When selecting the right CNC machining tolerances for a given application, it is important to consider all of the factors outlined below. It is also helpful to discuss these details with an experienced machinist in order to ensure that the right tolerance is specified and that the part can be manufactured as required.
– Product Application: The design and use of the product can have an impact on what tolerance should be specified. For parts used in the medical or aerospace industry, tighter tolerances are necessary in order to meet the requirements of these industries. So you will have to understand the requirements of your application thoroughly. This will help you to determine what tolerance levels are appropriate for your parts.
– Material Properties: Different materials will require different tolerances in order to achieve the desired performance. For example, soft materials like plastics are easily deformed after they are taken off the machines, they may require additional fixtures to achieve specified tolerances after machining like re-shaping. While hard materials like steel or aluminum need tighter tolerances in order to maintain their shape.
– Cost: Tighter tolerances are more expensive to produce and may not always be necessary for certain applications. Depending on the complexity of the part, different levels of tolerance can dramatically affect the cost of production.
– Operator Skill: Experienced operators are better able to produce parts with tighter tolerances than less experienced ones.
– Surface Finishing: The finishing process can also affect the desired tolerance. For example, parts to add plating, powder coating or hard anodizing will affect the final dimensions and this factor should be considered when specifying tolerances.
– Manufacturing Methods: Different manufacturing methods will require different tolerances. For example, parts made with additive manufacturing processes such as 3D printing will usually have looser tolerances than those machined with traditional methods.
– Final Inspection: When you design a part, you must consider how to do a final inspection process. It is important to consider the type of gaging and inspection equipment available, as this will affect the tolerances that can be achieved.
By considering all of these factors, designers can ensure that their parts are produced to meet their expectations in terms of quality and performance. Additionally, choosing the right CNC machining tolerances can help to reduce manufacturing costs by using less material and preventing unnecessary rework or scrap parts.
FAQs About CNC Machining Tolerances
Q: When do You Need Tight Tolerances?
A: Tight tolerances are usually required for applications such as medical, aerospace and automotive parts where precision is essential. These parts need to be machined with close tolerances in order to maintain their accuracy and performance.
Q: How can I improve CNC accuracy?
A: You can improve CNC accuracy by ensuring that the parameters used in the program are correct, that the machine is properly calibrated, and that all material is securely clamped during machining. Additionally, experienced operators with a good understanding of the CNC process will be able to produce parts with better accuracy.
Q: What Is Parallelism?
A: Parallelism is an important dimension when specifying CNC machining tolerances. It refers to the degree of flatness between two surfaces in relation to each other. If parts are not parallel, they may not fit properly together when assembled.
Q: What Is Perpendicularity?
A: Perpendicularity is a measure of the angle between two surfaces. It is important to consider when designing parts that need to fit together precisely, such as medical implants or automotive components. Parts with tight perpendicularity tolerances will ensure a secure fit and avoid unwanted gaps.
Q: How Can I Minimize Cost?
A: To minimize cost, it is important to consider the complexity of the part and choose an appropriate tolerance level. Tight tolerances can add to the cost of production, so it is important to choose one that is suitable for the application. Additionally, experienced operators and well-maintained equipment can help reduce costs by producing parts with fewer defects or scrap material.
Q: How is CNC accuracy measured?
A: CNC accuracy is typically measured in terms of the tolerance levels achieved for features such as roundness, parallelism, and perpendicularity. A part’s overall accuracy will depend on these individual measurements and must be taken into consideration when specifying CNC machining tolerances.
Examples of How to Apply CNC machining Tolerances in Practice
– Automotive: Automotive parts require tight tolerances to ensure that components fit together properly and safely. For example, wheel hubs must have precise diameters in order to fit the wheel bolts securely. Tighter machining tolerances can also be used for critical surfaces, such as brake pads or engine components, which must be flat and parallel in order to function correctly.
– Medical: Tight tolerances are essential for implants and other medical components that need to fit together precisely in order to work effectively. For example, hip replacements must have close tolerances for the surfaces that join the implant to the patient’s bones.
– Aerospace: In aerospace applications, tight machining tolerances are necessary to ensure the safety of passengers and crew. For example, aircraft wings must have precise surfaces that are parallel and flat in order to reduce drag and improve fuel efficiency.
By understanding the principles behind CNC machining tolerances and considering all relevant factors, designers can achieve the best possible results for their parts. Additionally, experienced CNC operators and high-quality machines are essential for producing parts with the desired accuracy.
Shanghai Elue, Your Partner for Professional CNC Machining Services
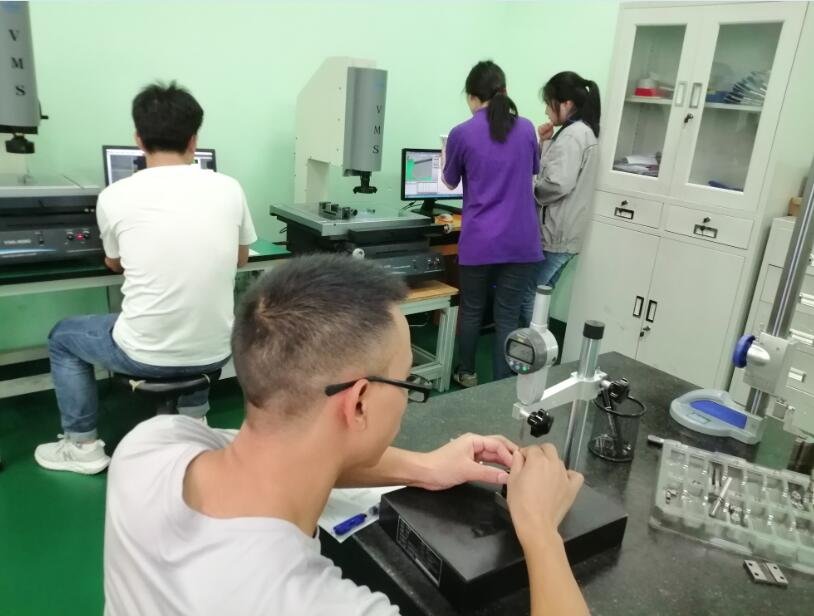
At Shanghai Elue, our experienced professionals understand the importance of precision and accuracy when it comes to CNC machining. We are dedicated to providing the best quality parts for our customers and work closely with them to ensure that their project meets their exact requirements. With our high-precision machines, skilled operators, and strict quality control processes, we are confident in our ability to provide the best service and results. Contact us today to find out more!