Product manufacturing has been a crucial concern for manufacturers in terms of process and cost optimization. In recent years, the competition between different industries has grown extensively. That results in varying and complex design demands.
For example, if we talk about the automotive industry. In 1886, Carl Benz applied for a patent for his three-wheeled gas engine vehicle. The revolution occurred when commercial manufacturing of cars started on a large scale and was accessible to the masses. At those times, cars were manufactured with human hands. But in the current age, despite the technological advancement, rapidly evolving manufacturing requirements of consumers are a big problem.
To resolve this issue, the term design for the assembly was introduced. It ensures that manufacturers can meet the never-ending demands of their customers from different industries. Design for manufacturing and assembly is the method for process and cost optimization of the manufacturing process. While minimizing assembly operations, which assists in eliminating component redundancy, facilitates assembly and manufacturing of products that are cost-effective in terms of material requirements, parts production, labor, and overhead.
In this article, we will discuss design for assembly and manufacturing, their difference, and the importance and benefits of design for assembly. In the end, some important tips for an effective design for assembly will be introduced.
What Is Design for Assembly (DFA)?
Design for assembly (DFA) is a process that involves ease of product design by minimizing the number of assembly operations. Thus offering reduced costs and ease of assembly.
Lesser assembly parts in product manufacturing are important and have an added advantage. Such as if a product has fewer parts it will reduce the time to assemble and assembly costs. Design for assembly assists designers and manufacturers in product design optimization before we start the actual production. Thus providing us with numerous advantages.

The predominant objective to implement DFA is cost-effectiveness and minimizing the number of assembly operations. Where it is applied in product design before production, it shows remarkable improvements in the product’s quality, accuracy, and durability.
Applications of Design for Assembly (DFA)
Design for manufacturing and assembly find their application across different manufacturing industries specifically the ones relating to consumer product design. It is rapidly adaptive in such manufacturing fields where manufacturing demands are in bulk. But at the same time, high precision, manufacturing efficiency, durability, and cost-effectiveness are mandatory.
Different industries might have their own intent to implement design for manufacturing and assembly. That depends on their industrial and consumer requirements. Some industries implement it as a compulsory requirement. Their intent of implementation might be cost-effectiveness and processing accuracy. But some might incorporate DFA principles into their product development processes to reduce labor costs.
It does not concern what objectives different industries possess to incorporate DFA. As for as product development processes optimization is concerned, it can wonderfully fulfill the diversified demands of every manufacturing industry.
Differentiate DFA and DFM
When it comes to improvements in a product’s design and its functionality, there are two processes. Design for assembly (DFA) and design for manufacturing (DFM). By implementing these processes into product development, the demanded product attributes can be successfully achieved.
Design for manufacturing (DFM) focuses on the ease of manufacturing for a product’s constituent parts. It predominantly focuses on selecting the most cost-effective materials and processes to be used in production. Thus minimizing the complexity of the manufacturing operations. On the other hand, as discussed above, design for assembly (DFA) is a process that involves ease of product design by minimizing the number of assembly operations.
The common thing between both the processes is that they serve an alike objective of product’s design and functionality improvements. But they differ in the following manners.
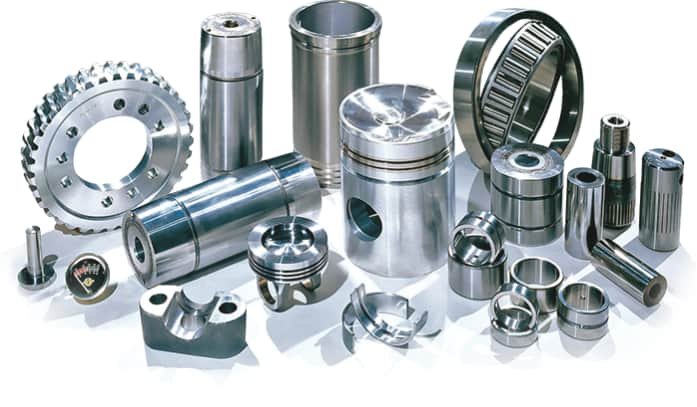
DFM focuses on the ease of manufacturing for a product’s constituent parts. Whereas, DFA involves ease of product design by reducing the number of assembly operations.
DFM is incorporated to minimize the complexity of the manufacturing operations. But DFA offers cost-effectiveness and ease of assembly.
Design for assembly and Design for Manufacturing are both employed simultaneously in manufacturing processes. This is cumulatively referred to as DFMA (i.e. design for manufacturing and assembly).
Benefits to Incorporate Design for Assembly in Manufacturing
Incorporating DFA principles into your product development processes offers numerous benefits that are discussed below
1, Offers Reduction in Production Time
One of the major benefits to implement DFA is that it offers a reduction in part production time. Because it helps in product design optimization and eradicates unnecessary steps and revisions. Which ensures the elimination of delays in the production process and speeds up the whole manufacturing process.
2, Offers Cost-Effectiveness
Incorporating DFA principles into your product development processes ensures cost-effectiveness. It just happens because of minimizing the number of assembly operations.
3, Eliminates Wastage of Material
DFA eliminates multiple trials during production. Thus optimizes wastage of material during production.
4, Offers Manufacturing Durability and Product Reliability
The design of assembly offers manufacturing durability and product reliability because it helps to minimize the number of assembly parts before production. That minimizes the chances of parts failure.
5, Offers Automation
Since all the assembly parts are self-aligned through robots that provide automation. Which is helpful in comparison to manual assembly alignment.
Guidelines to Implement Design for Assembly
There are numerous guidelines for design for assembly to incorporate it in production processes. The important ones are discussed below
Minimize Part Count
If you want to rapidly up to your product assembly then you need to minimize your part count. Minimizing part count should not be overused. Use it carefully wherever possible. The rule to part count minimization is that it should not disturb the functionality and features of the final part.
Remember one thing, while minimizing part count you cannot disturb its features and functionality. By reducing part count, you will be able to reduce the number of fasteners that would be cost-effective. Which ultimately results in a faster final assembly.
Introduce Fasteners in Product Design
You should introduce fasteners in the product design to increase assembly production speed. You should directly integrate fasteners rather than using screws that are more time-consuming and require more labor to assemble.
To introduce fasteners, you can use snap-fits and living hinges that are easy to use and quick. While in some cases, screws might be mandatory but you should try to eradicate them wherever you can.
Focus on Part Symmetry
Part symmetry is absolutely important because symmetry and assembly go along with each other. If your parts are symmetrical then labor working on the assembly line can easily assemble them without any problem and delay. Otherwise, it would create hurdles for them and can slower the product’s assembling process.
Manufacturing asymmetrical parts will confuse the technicians to use the proper tool. It also increases your tooling costs for assembling parts of different sizes. Therefore, it is guided that use symmetrical parts for faster assembling.
Avoid the Wrong Installation of Parts
To optimize the assembly process, the wrong installation of the parts should be avoided. If even one part is installed wrongly, it would disturb the whole assembly line. Which might be resulting in delays and inefficiencies.
To avoid the wrong installation of the parts, the self-aligning feature can be introduced. It uses robots for alignment. That ensures the efficiency of the assembly process and is cost-effective in terms of labor reduction.
Keep Things Simple
You should avoid any complexity in the product design. Try to keep things simple. It will help other team members to understand the process and confusion can be avoided. That will be ultimately beneficial for part assembly production. You should prefer a simple design that can perform the same task as a complex one can do.
Another benefit to keeping design simple is that it would require lesser constituent parts to be manufactured for the final part production.
Conclusion
If you want your part assembly production to be cost-effective, efficient and wish your final part to be reliable, then you must incorporate the design for assembly (DFA) principle into your product development processes. As discussed above, DFA finds its application in many manufacturing industries. It offers numerous benefits.
If you are looking for a CNC machining workshop and need high-precision custom-designed parts then JUST CONTACT US. You can get our world-class and advanced CNC machining services. We are amongst China’s top-rated CNC machining workshops with the ISO9001 certificate.