Edm And Wire Edm Machining are terms used in the manufacturing world to describe two very specific types of machining. Both involve the use of electricity to create or remove material from a workpiece, but they differ in the way that electricity is applied.
With EDM, a thin wire is passed through a dielectric fluid and then brought into contact with the workpiece. This creates an electrical discharge that erodes the metal. With wire EDM, a continuous coil of wire is fed through a bath of dielectric fluid and then dragged across the surface of the workpiece. This creates an arc between the wire and the workpiece that vaporizes the material. Both processes are precise, fast, and reliable.
What is EDM Machining and Its Applications
EDM machining uses an electrical current to melt the metal being cut. An electrode is used to discharge electrical sparks that heat and vaporize metal in a controlled manner. The molten material then falls away from the workpiece, which results in a clean surface finish with very low levels of stress or burrs.
In EDM, a high-powered pulse of electricity is used to melt or cut the metal. This process is often used to remove material from the metal surface. It is a versatile and subtractive manufacturing process to remove material from a workpiece through Electric Discharge that always excels at cutting through very difficult materials. This technology is typically used for the creation of prototypes, parts, and tools.
EDM enables designers to create parts quickly, easily, and cost-effectively. It is particularly useful for creating high-precision, multi-material parts that could not be made by other means.
EDM can machine virtually any conductive material, including stainless steel, nickel, titanium, and alloys of aluminum, copper, iron, and many other metals. Electrical Discharge Machine (EDM) uses an electric current to make sparks that are highly capable of eroding the workpiece. Below are the advantages and disadvantages of this process.
EDM has the ability to create precise and unique shapes, and it has been used by various industries in their manufacturing processes. Below are some typical applications for EDM:
Mold Cavity Making:
EDM cavity processing includes forging die, die-casting die, extrusion die, plastic molds and so on. Cavity machining is difficult, mainly because it is not through-hole machining, metal erosion is large, working fluid circulation and the removal conditions of corrosion products are poor; the 2nd reason is that the cavity is very complex, and the electrode loss is not uniform, which greatly affects the machining precision, so the cavity processing productivity is low, and quality is difficult to guarantee. In order to improve the processing accuracy of the cavity, highly corrosion-resistant pure copper and graphite must be used as electrodes.
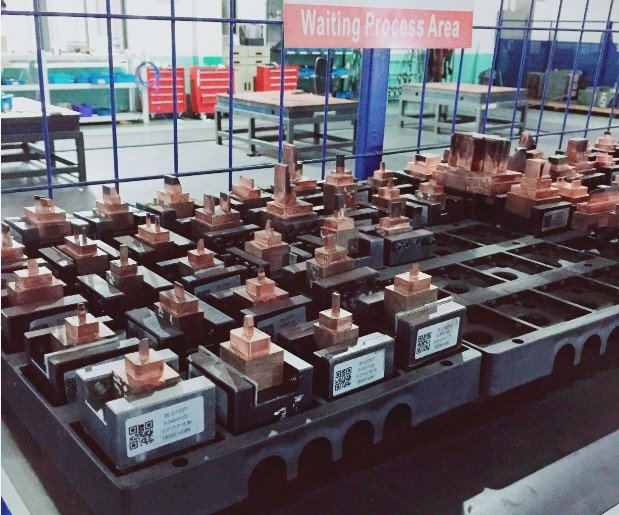
Electric Spark Perforation:
Perforating is the most widely used type of Electrical discharge machining. It is commonly used for machining a variety of complex shapes of hole workpieces, including round holes, square holes, special-shaped holes, curve holes, thread holes, deep holes, etc
The dimension accuracy of the hole is ensured by the size of the tool electrode and the gap between the spark discharge and the hole, its dimension accuracy is one level higher than the workpiece, generally not lower than IT7 level, while the surface roughness is smaller than the workpiece, and the straightness, flatness, and parallelism are not greater than 0.01 mm in 100mm length.
What is Wire EDM Machining and Its Applications
Wire EDM is also known as wire-cut EDM, wire cutting, or electrical wire erosion. It is a method of machining that uses a thin wire to cut through metal. The wire is extremely thin, so it’s able to slice through the metal without creating high levels of friction or heat. This results in a smooth surface finish and very minimal burrs.
EDM has many applications, ranging from medical, automotive, and aerospace manufacturing to intricate jewelry designing. It can be used for cutting intricate shapes in hard-to-reach places that are difficult or impossible to machine with conventional methods. Some typical applications for wire EDM include:
• Creating intricate shapes in dies, molds, and other workpieces that are difficult to reach with conventional machining methods.
• Precision cutting of hardened metals such as stainless steel, titanium, and cobalt alloys.
• Cutting delicate components for medical device manufacturing.
• Making small, complex parts with high accuracy and low surface roughness.
• Creating intricate shapes, slots, and holes in components made from thin sheet or plate materials.
Wire EDM can provide significant advantages over traditional machining methods, including reduced tooling costs, improved quality, increased production rates and improved productivity.
The wire EDM process is suitable for machining all kinds of difficult-to-machine materials, such as alloy tool steel, titanium and cobalt alloys, etc., which have high hardness and high wear resistance. It can also be used for machining hardened materials that are not suitable for conventional machining methods, such as ceramics, carbides and composites. In addition, it can also be used to cut or shape small components with very tight tolerances.
In conclusion, EDM and wire EDM machining are two of the most advanced and accurate machining methods today. EDM is suitable for machining the cavities of precision dies and molds, while wire EDM can be used to cut complex shapes in hard-to-reach places, as well as small components with high accuracy and low surface roughness. Both processes offer significant advantages over traditional machining methods, including reduced tooling costs, improved quality and increased production rates. By using EDM or wire EDM, parts can be made quickly and accurately with minimal burrs.
In addition to the above-mentioned advantages, both EDM and wire EDM require only a few common materials to operate, such as copper wire and graphite electrodes. Furthermore, these processes don’t require coolants to machine materials. This eliminates the need for an additional cooling system and reduces production costs. Therefore, both EDM and wire EDM are cost-effective solutions for producing complex parts with high accuracy and low surface roughness.
The Difference between Edm and Wire Edm Machining
The main difference between EDM and wire EDM machining is the method used to cut through metal. EDM uses electrical discharges, while wire EDM uses a thin wire. Each method has its own advantages and disadvantages, depending on the type of material being cut.
In EDM, a metal workpiece is placed between two electrodes. An electrical current then passes through the metal, causing sparks to erode the material away.
Wire EDM works by passing a special wire through the material in order to cut it into shape. This process relies on an electric spark for completing the job more quickly than traditional machining methods.
They both can be used to create complex shapes with tight tolerances that would be difficult to achieve using other machining processes, making them ideal for creating parts with complex geometries. Additionally, they both have the benefit of being able to machine materials that are otherwise difficult to work with, such as hardened steel and other hard metals.
As a result, both EDM and wire EDM have become popular choices for the production of automotive, aerospace, medical, and other industrial components. By providing a level of accuracy not obtainable by conventional methods, these processes are helping to increase the quality and efficiency of machining operations around the world.
Pros and Cons of EDM and Wire EDM Machining
The main advantage of EDM and wire EDM machining is their ability to produce complex parts with high accuracy. Additionally, they are capable of cutting through hard materials that would be difficult to work with using other methods.
However, there are some drawbacks associated with these processes as well. EDM requires special electrodes that need to be replaced regularly, which can add to the cost of the machining operation. Additionally, EDM is not suitable for large-scale operations due to its slow speed.
Wire EDM requires a specialized wire that must be replaced frequently, and the process can be time-consuming. Additionally, it is limited in terms of size and complexity.
Overall, both EDM and wire EDM can be beneficial for certain applications. By understanding the pros and cons of each method, manufacturers can make an informed decision when deciding which process is best suited for their needs.
How to Choose the Right Machining way for Your Needs
EDM and wire EDM offers a number of advantages over traditional machining methods. Their ability to produce complex parts with precision and speed makes them an ideal choice for many types of applications. While each process has its own unique advantages, it is important to consider all factors before making a decision in order to ensure that the most suitable method is selected. By taking the time to research and evaluate both EDM and wire EDM processes, manufacturers can make sure that their machining operations are running in the most cost-effective manner.
Many factors must be taken into consideration when deciding between EDM and wire EDM machining. The cost of the electrodes, for example, must be taken into account when choosing an EDM process. Additionally, it is important to consider the size and complexity of the workpiece to ensure that the desired results can be achieved with either method. It is also essential to consider the level of accuracy required as well as the amount of time and effort needed for the machining operation. By evaluating all of these factors, manufacturers can make an informed decision when it comes to selecting the right process for their needs.
Overall, both types of machining are widely used in the manufacturing industry and can be used to produce highly accurate results. The choice between the two types depends on the application and the type of material being cut.
Conclusion
EDM and wire EDM machining are both extremely useful processes for producing highly accurate parts. Each offers its own unique advantages, so it is important to take the time to research and evaluate both methods before making a decision. By considering all of the factors mentioned above, manufacturers can choose the best method for their needs in order to ensure that their machining operations are running in the most efficient and cost-effective manner. With the right process chosen, manufacturers can experience greater production efficiency and improved product quality.
At Shanghai Elue, we provide both 2 processing methods. We are happy to help you find the right process for your needs. With our specialist knowledge, we can ensure that your machining projects run smoothly and with maximum efficiency. Contact us today to learn more!