Heat sinks are essential components for dissipating the heat generated by electronic components. Without them, devices will overheat and eventually fail. Heat sinkers come in a variety of shapes and sizes to suit different applications, from small cooling fins on processors to large aluminum blocks used in industrial systems.
With so many options available, it can be difficult to know which one is best for your application. This guide aims to provide an overview of the different types of heat sinks, their advantages and disadvantages, and how they should be installed properly for optimal performance.
What is a Heat Sinker & How it Works?
A heat sink is a device used to dissipate the heat generated by an electronic component or system. Heat sinks are often made of metal, such as aluminum or copper. They are commonly attached to components that require cooling, and the most common application for heat sinks is in computers where they are used to cool processors and other components.
A heat sink works by transferring the heat generated by an electronic component or system away from that component or system and into the surrounding environment. Heat sinks use conduction to transfer the heat, meaning they employ something such as metal rods to move the heat away from the component or system. Heat sinks also have fins, which increase the surface area of the sink and allow for greater heat dissipation.
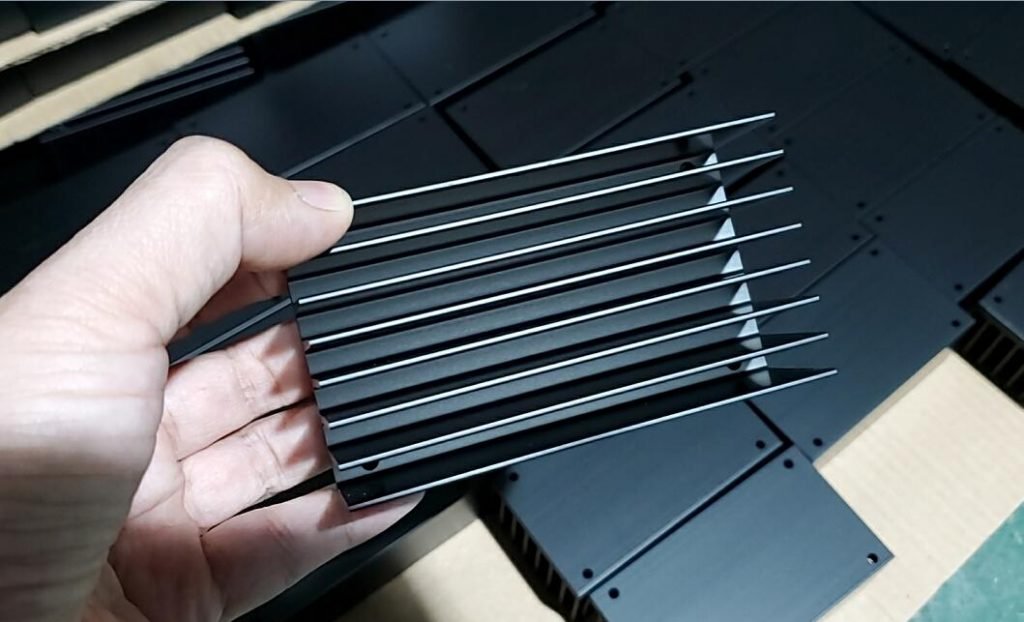
Heat sinks provide several benefits to both users and manufacturers alike. For instance, by dissipating heat away from components, heat sinks can help to extend the lifespan of those components as well as reduce their energy consumption.
Additionally, heat sinks provide a cost-effective solution for cooling since they require no additional power source or maintenance.
Different Types of Heat Sinkers
There are several different types of heat sinks available on the market today. The most common type is the active heat sink, which uses an internal fan to draw air away from the component or system, thus cooling it. Other types of heat sinks include passive heat sinks, which rely on convection for cooling, and thermoelectric coolers, which use a combination of electrical current and thermal energy to dissipate heat.

Depending on the outer shape, there are 3 main types of heat sinks.
Pin-fin heat sink: It uses a series of thin metal fins to dissipate heat. The pins create turbulence in the air due to their size, allowing for more efficient heat dissipation.
Plate fin heat sink: It is similar to the pin-fin heat sink but uses rectangular plates instead of pins. This type of heat sink is more efficient due to its larger surface area and better airflow.
Flared fin heat sink: The flared fin heat sink is shaped like a cone, which helps to maximize the surface area exposed to air. This type of heat sink works better in confined spaces due to its shape.
Different Ways to Manufacture Heat Sinks
Heat sinks can be manufactured in a variety of ways, depending on the application. The most common methods are extrusion, die-casting, and stamping. Extrusion is the process of pushing heated metal through a die which forms it into desired shapes. This method is used for heat sinks with complex geometries such as pin-fin or flared-fin heatsinks.
Die-casting is another popular manufacturing technique where molten metal is injected into a mold and allowed to cool before being removed from the mold. This method offers greater flexibility than extrusion because it allows for more intricate designs and smaller parts to be created quickly and cost-effectively.
Finally, stamping involves pressing heated metal sheets between two dies to form various shapes or features on the sheet material – this technique works well for flat plate-fin heat sinkers that require large surface areas but little complexity in design or geometry.
- Skived heat sink: This type of heat sink is made by skiving or slicing material from a single piece of aluminum or copper to create a finned surface with many small surface areas for efficient heat dissipation.
- Extruded heat sink: It is made of aluminum or copper and formed using an extrusion process. This type of heat sink can be designed to fit any shape or size, allowing for great flexibility in its design. Additionally, it can also be customized with fins and other features to further improve its cooling capabilities.
- Casting heat sink: Casting is a way of making a heat sink from molten metal. By pouring the molten metal into a mold, it is possible to create intricate shapes and designs for your heat sink. This type of heat sink is often made of aluminum or copper, and It is generally more expensive than extruded heat sinks, but it offers much greater control over the shape and design of the heat sink. This makes it perfect for applications where a precise fit is needed.
- CNC Milling heat sinks: This type of heat sink is machined from a solid block of aluminum or copper. By using CNC milling, the heat sink can be customized to any shape or design. This type of heat sink is often used in applications where the highest level of precision is required. Additionally, it can be designed to have very high surface areas for greater cooling capabilities.
FAQs About Heat Sinkers
Q: How to Choose a Heat Sinker
A: When selecting a heat sink, there are several factors to consider such as the size and shape of the component or system that needs cooling, the amount of power it requires, and the type of environment in which it will be used. Additionally, some heat sinks may require additional fans or other cooling features in order to function properly. Ultimately, the right heat sink for your application depends on its specific requirements and the environment in which it will be utilized.
Q: What is the Difference Between Passive and Active Heat Sinks?
A: Passive heat sinks rely on convection for cooling, while active heat sinks use a combination of electrical current and thermal energy to dissipate heat. Active heat sinks are more efficient but require additional power and can be more expensive.
Q: Are Heat Sinkers Necessary?
A: Yes, heat sinks are necessary for any electronic component or system in order to keep it from overheating and malfunctioning. Without a heat sink, components are likely to suffer from accelerated wear and tear due to extreme temperatures. Additionally, using a heat sink can extend the lifespan of your device significantly.
Q: What Factors affect heat sink performance?
A: Heat sink performance is largely dependent on the material it is made from, its shape and size, the amount of exposed surface area, and any additional cooling features like fans or liquid coolers. Additionally, environmental factors such as ambient temperature and air circulation can also affect heat sink performance.
Q: What are the Different Types of Heat Sinkers?
A: There are several different types of heat sinks available, including extruded, casting, and CNC milling. Each type offers its own unique benefits and can be beneficial in certain applications. Ultimately, the right design for your application depends on its specific requirements and the environment in which it will be used.
Q: What are the Benefits of Using a Heat Sink?
A: Heat sinks offer several benefits such as increased lifespan, improved overall system efficiency, and better heat dissipation. Additionally, they can reduce noise levels significantly and help to keep components at optimal temperatures for optimum performance. Ultimately, using a heat sink can save you money in the long run, while also helping to extend the life of your system.
Q: What are the Disadvantages of Using a Heat Sink?
A: The main disadvantage of using a heat sink is that they can be expensive and may require additional cooling features such as fans or liquid coolers. Additionally, some types of heat sinks may be too large for certain applications, which can limit their effectiveness. Heat sinks also require regular maintenance and cleaning in order to perform at optimal levels.
Q: Are Heat Sinkers Environmental Friendly?
A: Heat sinkers are made from materials that are generally considered to be environmentally friendly and do not release any harmful toxins into the atmosphere. Additionally, some heat sinks are designed to be more energy-efficient than others, which can help reduce your overall carbon footprint. Ultimately, using a heat sink can help protect both your system and the environment.
Conclusion
Heat sinks are essential for any electronic component or system to function properly and efficiently, and they offer a number of benefits such as increased lifespan and energy efficiency. There are several different types of heat sinks available, each with their own unique characteristics that can be beneficial in certain applications. Overall, understanding the differences between the types of heat sinks and choosing the right one for your application can help ensure that your system runs smoothly while also saving you money in the long run.