Machinability is the measure of how easily a material can be cut, shaped and formed into a finished product. It’s an important factor to consider when selecting materials for any type of manufacturing project. With proper machining techniques and tools, metals, plastics and other materials can be machined with high precision and accuracy. In this guide, we’ll explain what machinability is and provide tips on how to achieve it. We’ll also discuss the different factors that affect the machinability.
What is Machinability
Machinability is the ability of a material to be machined or worked with cutting or forming tools. It refers to the ease and efficiency with which a particular material can be cut, formed, drilled, reamed, tapped or otherwise manipulated using machine tools. In general terms, materials that are more difficult to work with have poorer machinability, while those that are easier to manipulate have higher machinability.
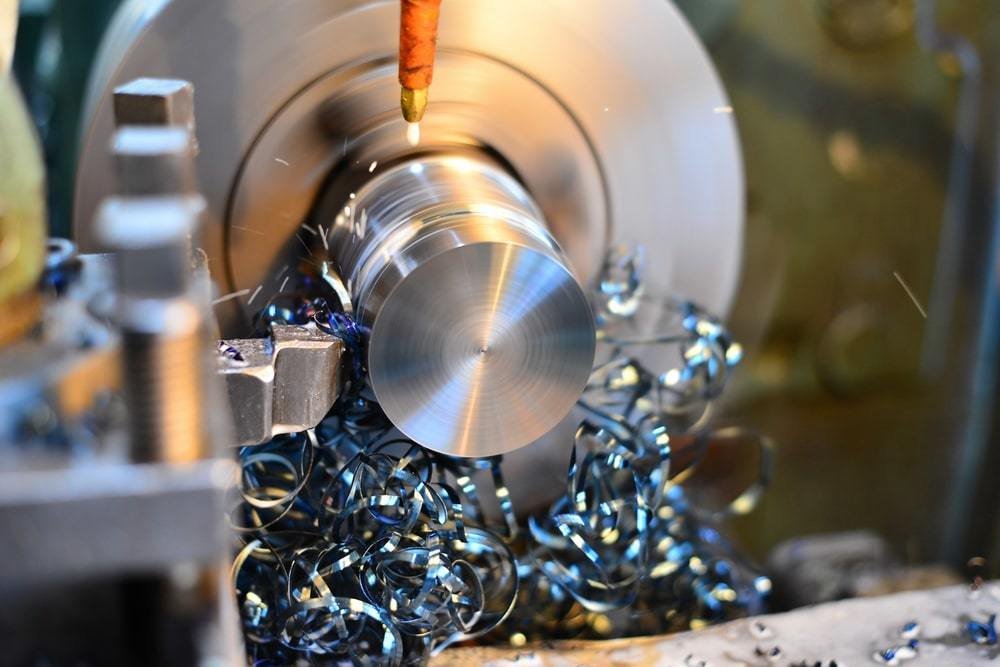
Factors That Impact Machinability
The factors that impact the machinability of a material include its hardness, chemical composition, grain structure and heat treatment.
–Hardness
Harder materials require more energy to machine compared to softer materials, so they are generally more difficult to work with and have poorer machinability.
–Chemical composition
Materials that are chemically complex can also be difficult to machine as it can be hard to predict how the material will react when being cut or formed. For example, metals with high levels of carbon and alloying elements tend to be more difficult to machine than those with lower levels.
–Grain structure
The grain structure of a material is also important; materials with larger, coarser grains or irregularly shaped grains tend to be more difficult to machine than those with finer, more uniform grains.
–Heat treatment
Heat treatment can also impact machinability as materials that have been heat treated may be harder and more difficult to machine than those that have not been processed in this way.
5 Main Types of Machining Methods
There are several methods of machining a material, depending on the shape and size of the workpiece, and the tools being used. The most common machining methods are milling, drilling, turning, grinding and honing.
-Milling: Milling is a process of cutting away material from a workpiece using an endmill or similar tool in a rotary motion. It is most commonly used for producing flat surfaces, slots, holes, and other shapes in components.
-Drilling: Drilling is a process of creating round holes or indentations in a workpiece using a drill bit to rotate and remove material.
-Turning: Turning is a form of machining that involves rotating a component against an abrasive tool to shape it.
-Grinding: Grinding is a process of removing material from a workpiece by abrading it with an abrasive wheel. It can be used to create very precise shapes and sizes in components.
-Honing: Honing is a type of finishing process where the surface of the component is made smooth and even using an abrasive stone. It is commonly used to improve the surface finish of components and increase their accuracy.
Different Types of Machinable Materials
The materials that can be machined vary greatly depending on the type of tool and method used. Commonly machinable materials include metals such as steel, brass and aluminum, as well as plastics.
- Steel: Steel is one of the most commonly machinable materials. It can be machined with a variety of tools and techniques to produce precise, accurate components.
- Brass: Brass is an alloy of copper and zinc, making it relatively soft and easy to work with. It can be machined using a wide range of tools, including drill bits and end mills.
- Aluminum: Aluminum is a lightweight metal that is easy to work with and can be machined quickly using conventional tools. It is often used in aerospace applications due to its corrosion resistance and lightweight.
- Plastics: Plastics are relatively soft materials that can be machined easily using specialized cutting tools such as end mills. However, the type of plastic being machined will determine the exact tools and techniques required.
Commonly Used Metrics for Measuring Machinability
When assessing the machinability of a material, several metrics are commonly used to measure its performance. These include:
-Surface finish: This is a measure of how smooth and even the surface of the workpiece is after machining. It is usually measured in microns or millimeters and higher numbers indicate better machinability.
-Cutting speed: Cutting speed is a measure of the rate at which material is removed from the workpiece when machining. Higher cutting speeds indicate better machinability.
-Tool life: Tool life is a measure of how long a tool lasts before it needs to be replaced due to wear and tear. Longer tool life indicates better machinability.
-Power consumption: Power consumption is a measure of how much energy is required to machine the material. Lower power consumption indicates better machinability.
-Scrap rate: Scrap rate is a measure of how much material is wasted during machining, with higher scrap rates indicating worse machinability.
Machinability is an essential concept to understand when designing a component, as it will determine the type of material and machining approach used. The metrics outlined above are commonly used to assess the machinability of different materials and they should be taken into consideration when selecting a material for a particular application. Understanding the machinability of material will help ensure the production process runs smoothly and efficiently.
Tips to Improve Machinability of Materials
1. Use the correct cutting tools for the material: Different materials require different types of cutting tools to achieve optimal performance. For example, harder materials such as steel will require carbide-tipped or diamond-coated tools, while plastics should be machined with high-speed steel (HSS) tools.
2. Use the proper cutting speeds: The speed that a tool is moved across the material being machined will impact its performance. Faster speeds can produce smoother surfaces, while slower speeds are better for more intricate shapes and contours.
3. Use coolants or lubricants when necessary: Coolants or lubricants should be used when machining certain materials in order to reduce friction and improve the performance of the cutting tool.
4. Choose the right type of clamping: Clamping is an important factor in machining materials as it helps ensure accuracy and prevent damage to the workpiece or tooling. The correct type of clamping should be chosen based on the material, size and shape of the workpiece.
5. Use the proper feeds and speeds: The feed rate, or the speed at which a tool is moved across the material, should be adjusted to match the type of material being machined. Slower feeds are generally recommended for harder materials and higher feeds for softer materials. Similarly, faster spindle speeds should be used for harder materials and slower speeds for softer materials.
6. Utilize chamfers and radiuses when needed: Chamfers and radiuses are angled surfaces that can often improve the performance of cutting tools by reducing stress concentrations at sharp edges or corners. They should be used when machining certain materials in order to extend tool life and improve performance.
7. Use the correct coolant or lubricant: Coolants and lubricants are generally used when machining materials in order to reduce friction, heat and wear on cutting tools. The type of coolant or lubricant that should be used will depend on the material being machined and the type of tooling being used.
8. Regularly check tooling condition: Tooling should be checked regularly to ensure that it is in good working condition. If the tools are worn or damaged, they should be replaced as soon as possible in order to avoid damaging the workpiece or producing inaccurate parts.
By following these tips and making sure you use the correct tools and techniques for the material being machined, you can ensure that your parts will be machined accurately and efficiently. With the right knowledge and experience, any material can be machined to produce precise components. The key is to understand the characteristics of each material and use the most suitable tools and techniques available.
Conclusion
Understanding the machinability of materials is essential when designing components. By taking into account the metrics outlined above, as well as following tips to improve the machinability of materials, you can ensure that your parts will be produced accurately and efficiently. With a complete understanding of material machinability, it is possible to achieve precise results in any machining project.