Manufacturing processes are the methods and techniques used to create products from raw materials. Manufacturing processes are used across many industries, including automotive, aerospace, medical devices, electronics, food processing and consumer goods. In this guide we will explore some of the most common manufacturing processes so that you can gain an understanding of how they work.
Overview of Manufacturing Processes
Manufacturing processes are the steps taken to transform raw materials into finished goods. There are many different types of manufacturing processes, they involve a range of complex operations, from assembly and fabrication to welding and machining. Each process has its own unique characteristics that require specialized knowledge and skill to ensure a successful product outcome.
6 Main Types of Manufacturing Processes
The most common manufacturing processes include casting, forming, machining, joining, and assembling.
Casting

Casting is one of the oldest manufacturing processes and it involves pouring molten materials into a mold to create the desired shape. After the molten material cools and solidifies, it can be removed from the mold for further processing. Some common examples of casting parts include engine blocks, gears, and structural components. This process is mostly employed with metals, while gravity casting, vacuum casting, die casting and sand casting are the common types.
-Gravity casting: This process uses gravity to fill the mold with molten metal. After the material cools and solidifies, it is removed from the mold for further processing.
-Vacuum casting: This process involves filling a mold with molten metal under a vacuum to ensure that no air is trapped in the part. Once cooled, the part can be removed from the mold and finished using various processes.
-Die casting: The metal is injected into an open or closed die cavity using extreme pressure.
-Sand casting: Molten material is poured into a sand mold and allowed to cool. After the material is removed from the mold, it can be machined or finished as desired.
Forming

Forming utilizes heat and pressure to reshape or deform raw materials into the desired product. Forming is a process that involves applying force to a sheet, strip, or another form of material in order to change its shape. The forming process can be done either manually or with machinery and is commonly used for making parts like car body panels, kitchen sinks, and aircraft wings.The main types of forming include extrusion, rolling, and forging.
-Extrusion: This process involves forcing a material, usually in the form of a bar or tube, through a die with an opening that forms it into the desired shape.
-Rolling: This process works by passing the material between two rollers that compress and shape it into the desired form.
-Forging: This process involves pounding or hammering a material into the desired shape.
Machining

Machining is a manufacturing process that involves cutting away material from a workpiece to create precise parts and components. This is done with a variety of cutting tools such as drills, saws, lathes, and milling machines. Machining is used to manufacture parts like engine blocks, manifolds, pistons, shafts, and other industrial components.
-Turning: This is a machining process that involves rotating the workpiece, while cutting tools are used to remove material from it.
-Drilling: This process involves using cutting tools to make holes in a workpiece.
-Milling: This is a type of machining operation in which a rotating tool removes material from the surface of the workpiece.
-Grinding: This process involves using abrasive wheels to remove material from the surface of a workpiece.
Joining

Joining is the process of fastening two or more pieces of material together. This can be done in several ways, including welding, soldering, riveting, brazing, and adhesive bonding. Joining is used in a wide range of manufacturing industries to assemble parts such as cars and airplanes.
-Welding: This process involves heating two pieces of metal and pressing them together tightly.
-Soldering: This process uses a filler material to join two metals at lower temperatures than welding.
-Riveting: This process involves driving a pin or rod through parts that are held in place by friction.
-Brazing: This process involves joining two pieces of metal using a filler material at a temperature that is higher than soldering but lower than welding.
-Adhesive bonding: This process involves using an adhesive to join two surfaces together.
Molding

Similar to casting, molding is the process of shaping molten material into a desired shape and size. This is done by forcing the molten material into a pre-made mold with the use of pressure or vacuum. There are 3 main types of molding, injection molding, blow molding, and compression molding. They are mainly used to make polymer parts such as plastic bottles, cups, toys, and electronic cases.
-Injection molding: This process involves injecting molten material into a pre-made mold.
-Blow molding: This process involves forcing molten material into a blow mold to form the desired shape.
-Compression molding: This is done by placing a two-part mold filled with hot, viscous material into an oven where heat and pressure are applied to form the desired shape.
Assembling
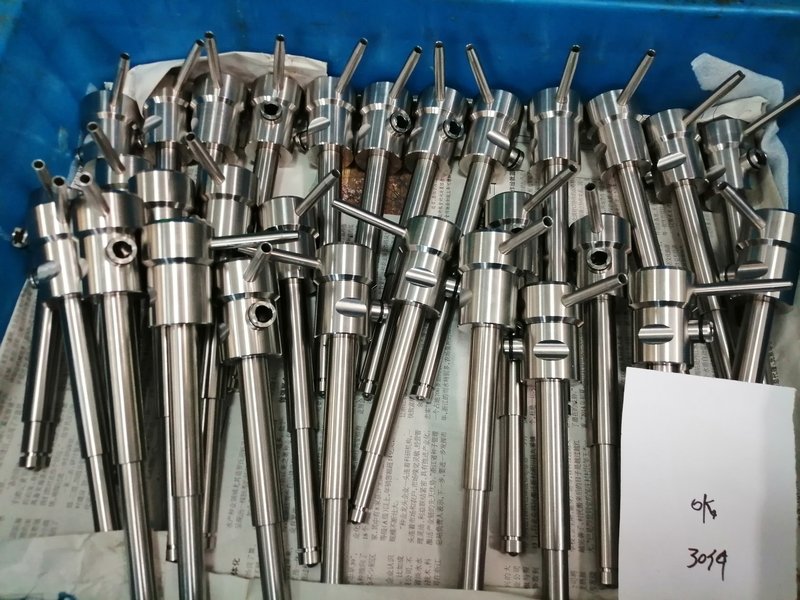
Assembling is the process of putting components and parts together to form a complete product, these include manual assemblies, automated assembly systems, and robotics. This process is used in industries such as automotive, electronics, furniture, and medical device manufacturing.
Overall, there are many different types of manufacturing processes that can be used to create a variety of finished goods. Each process requires specialized knowledge and skill to ensure a successful outcome, so it’s important to understand the basics of manufacturing before beginning any project.
Advantages and Disadvantages of Different Manufacturing Processes
Manufacturing processes are not all created equal, and each has its own unique advantages and disadvantages. It’s important to understand the pros and cons of a process before starting any project, as it can help determine which method is best suited for your needs.
Casting
Advantages: Casting has a wide range of applications, not limited by size, shape, weight, or complexity; production cost is relatively low; Casting can greatly reduce the post-processing cost.
Disadvantages: The casting structure is not compact enough, there are some defects like shrinkage, porosity, slag, crack, and uneven grain size; mechanical properties are low, and not resistant to big impact; scrap rate is a bit high because of the foundry production processes.
Forming
Advantages: High production efficiency with wide application, process easy to control, continuous and automatic production.
Disadvantages: Equipment is expensive and labor-intensive. The process may take a long time depending on the complexity of the part.
Machining
Advantages: High precision and accuracy, as well as good surface finish. Can create complex shapes with minimal material waste.
Disadvantages: Machining equipment is expensive. A resource-intensive process that requires skilled operators, specialized cutting tools, and fluids.
Joining
Advantages: Can create complex shapes with minimal material waste.
Disadvantages: Difficult to achieve consistent results, as the process relies heavily on operator skill and experience.
Molding
Advantages: It can produce complex shapes and accurate sizes with a short molding cycle, high production efficiency, and easy-to-realize production automation.
Disadvantages: Tooling cost is high, and not suitable for small batch production.
Overall, it is important to consider all factors before deciding which manufacturing process to use. Every situation will require different tools and resources, so a thorough understanding of the pros and cons associated with each process can help you make the best decision for your needs.
Factors to Consider When Choosing a Manufacturing Process
When it comes to choosing the right manufacturing process for your project, there are several factors to consider. By understanding each of these elements and how they impact the overall outcome of a product, you can make an informed decision that is best suited for your needs.
1. Order Quantity: The order quantity of the product will impact which manufacturing process you choose, as different processes are more suitable for large-scale or small-scale production.
2. Cost: Different processes can have vastly different costs associated with them, so it is important to consider this when deciding which one best suits your needs. The cost of materials, labor, and machinery should all be taken into account.
3. Complexity: Some processes are better at producing complex parts, while others may not offer the same level of precision or accuracy.
4. Time frame: The time frame required to produce the product will also help you decide which process is most appropriate. Some processes are faster than others, while some may require more setup time.
5. Material: Different processes may be better suited for certain materials than others, so it is important to consider the specific material you will be working with.
By taking all of these factors into account and understanding how they impact the overall outcome of a product, you can make an informed decision about which manufacturing process is right for your needs.
Conclusion
By having a clear understanding of the different manufacturing processes and their respective advantages and disadvantages, you can make an informed decision about which one is best suited for your needs. Consider all factors, including order quantity, cost, complexity, time frame, and material when deciding which process to use. With this knowledge in hand, you will be able to choose a process that is most efficient and cost-effective for your project.