Top Plastic Molding Supplier in China
Contact us today to start your next plastic molding project.
What is Injection Molding
Plastic injection molding is a process used to manufacture parts and components from thermoplastic materials. In this process, the molten material is injected into a custom-made mold at high pressure and temperature, where it cools until it solidifies. The molds are designed based on the customer’s specifications, and can be reused for future projects. Plastic injection molding is fast, efficient, cost-effective, repeatable and offers high precision with very little waste material. It also allows manufacturers to create large volumes of identical parts quickly and easily.
Additionally, plastic injection molding produces parts that are strong and resistant to corrosion due to their uniform composition throughout the entire part. This makes them suitable for a wide range of products, including medical devices, automotive parts and electronics. Plastic injection molding is an extremely versatile process that can be used to manufacture a variety of products with different shapes and sizes.
Our Molding Service
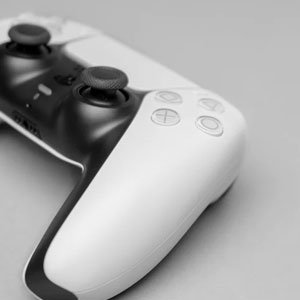
DFM report & Mould Flow analysis
Early involvement in customer products analysis, a detailed PPT will be provided
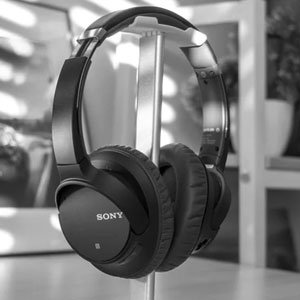
Rapid prototyping
before cutting molds, we’ll support on rapid prototypes to test designs from CNC machining or 3d printing

Mold design
As soon as you test prototypes, we work on mold designs and send you to approve before cutting molds
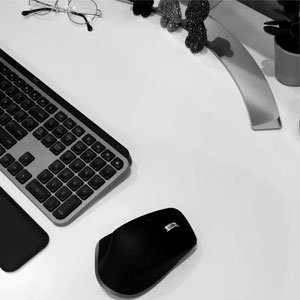
Mold testing & production
after mold designs get confirmed, we start on molds making and ship samples to confim again before production
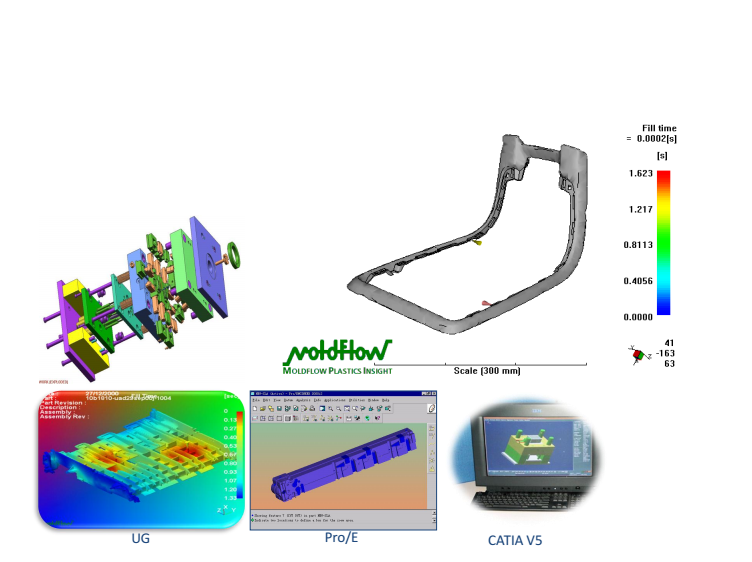
Injection Molding Materials
ABS: High impact resistance with low density,”Tough, hard, rigid, cheap”.The comprehensive performance is good and used widely in machinery, electrical, textile, automobile, aircraft, ships and other manufacturing industries and chemicals.
PA: High mechanical strength, good toughness, high tensile strength which is higher than metal and the compressive strength is close to metal. The impact strength is much higher than ordinary plastic.
PC: PC has good mechanical properties, but poor fluidity.The drying before injection is very important and the recommended drying conditions are 100C to 200C for 3 ~ 4 hours. The humidity before processing must be less than 0.02% .
PP: PP is a crystalline polymer. The density of PP is only 0.91 g/cm3(smaller than water) . In general purpose plastics, PP has the best heat resistance. and also good resistance to stress cracking and high bending fatigue life. The comprehensive properties of PP are better than those of PE.
PE: Polyethylene (PE) is the most widely used synthetic resin due to its excellent processability and serviceability
PC-ABS: The alloys of PC and ABS, PC has strong impact resistance, high heat resistance while ABS has very good toughness, so this material is better performance than a single PC or ABS and, more expensive.
POM: High crystalline polymer with high elastic modulus, high hardness and high stiffness. Can be used in-40-100 °C for a long time. It’s the most superior type among the thermoplastic material on fatigue resistance.
Injection Molds Surface Finish
We generally polish it a little with 800#sandpaper if no special requirement.
General use of stone, wool wheel or sandpaper, mainly done by manual. We can make it mirror polishing if requsted.
This texture is done by EDM Machining on the mold.
There are many types of the different texturing. and the often used here including MT11010, MT11020.
Electroplating is the process of depositing metal or alloy on the surface of a work piece by electrolysis to form a uniform, dense and well-bonded metal layer.
Sand blasting is a surface treatment of the workpiece process, using Compressed air as the power to form a high-speed jet to the surface of the mold.
Ready to start a new project ?
Advantages of Injection Molding
01.High Precision
Plastic molds can be made within +-0.02mm, which can meet the demand for most majorities.
02. Variety Materials
We can work from majority plastics like PP /PE/POM/ABS/PS/PC/PA, etc.
03. Low Costs
Injection molding is an automated process which can run 24hours without stop.
04.Complicated shapes & details
It's easy to make complicated parts from molds making.
05. Low Waste
Injection molding produces much less waste material which can be recycling.
06. More Strength
Injection molding parts perform better than cnc machining or 3d printing.
limitations of Plastic Injection Molding
Though there are many advantages to using plastic injection molding, there are some limitations associated with the process as well.
– The initial cost is big because you have to invest on customized molds, which makes it impractical for short runs or one-off products.
– This process is limited to thin wall parts and the thickness should be always consistent, as well as sharp corners that cannot exceed certain radii due to mechanical requirements. This limits how intricate the part design can be, especially when creating very small components.
– Additionally, injection molding requires a high upfront cost in terms of injection machines and labors.
The Process of Plastic Injection Molding
The first step of the plastic injection molding process includes creating the custom mold based on customer specifications and requirements. Once this is completed, raw plastic material—usually pellets or powder—is loaded into the hopper, which feeds it into the heated barrel of an injection machine. Here, the material is heated until it becomes liquid and can be injected through a nozzle at high pressure into the mold cavity.
Once filled with molten plastic, the mold is clamped shut and allowed to cool for a period of time. After cooling, the part is ejected from the mold and inspected for defects before being packaged and shipped to customers.
Insert Molding and OverMolding
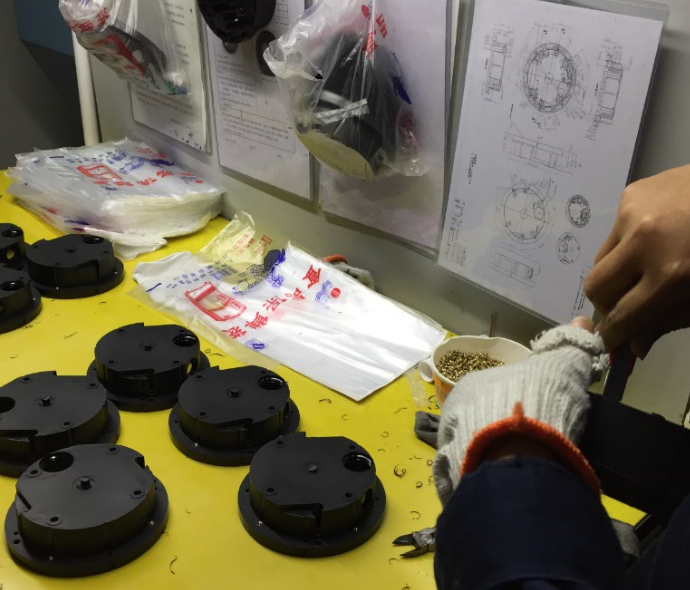
Insert molding is to have the metal insert pre-positioned in the mold and then injected into the plastic for molding, so that you can get a final product with an insert tightly embedded like a threaded ring,a brass nut or an electrode.
This type of molding will help to make parts all at once instead of post-assembly, especially when the inserts very small and quite a few ones on one part,it’ll save the assembly trouble a lot. also it’ll improve the product strength, since one-shot process will make the embedding very tight and easy to use.
Overmolding is actually one type of secondary injection molding which includes 2 parts,one is the main body (the hard plastic), and the other coating part (the soft one). When making molds we need to make the hard one first,and then put it into the coating mold.
The often used overmolding plastics as below
main body: ABS, GPPS, HIPS (475) , PA (PA6, PA66) , PC, PE, POM, PP, etc.
coating part: TPE, TPR, TPU, TPV, TPEE, PVC, etc.
