Choosing the right surface finish for your CNC machining parts is essential to ensure that they function properly and look good. In this article, we will discuss the different types of surface finishes and their applications. We will also provide tips on how to choose the right surface finish for your needs.
What is Surface Finish?
Surface finish is the final step in creating a CNC machined part. It refers to the overall look, feels and texture of the part after it has gone through the process of being cut or shaped by a computer controlled machine tool. The surface finishes for CNC parts vary depending on the material used, application and desired outcome. Generally, surfaces can be finished in one of ways: anodizing, painting and powder coating.
Surface finish is known as surface texture or surface topography, which is the nature of a surface as defined by the 3 common characteristics of lay, surface roughness, and waviness. Surface finish is frequently found on technical drawings for mechanical parts, and it is the desired result after machining. For example, surface finish “Ra3.2” stands for Roughness Average (RA) 3.2, which tells the machinist how much surface roughness is desired on the part after machining.
Different Types of Surface Finishes for CNC Machining Parts
The surface finish has three distinct elements:
Lay: The lay is the directional pattern in which a surface or material was machined. It includes irregularities such as circles, grooves, ridges, and furrows that are left behind after machining
Surface Roughness: The roughness of a surface can be determined by analyzing its microscopic features with specialized instruments. Generally, it refers to how even and consistent the surface is.
Waviness: This is determined by measuring the distance between peaks and valleys on a machined part’s surface. The waviness can be caused by vibrations during machining, as well as other factors.
Below are some most commonly used surface finishes at Shanghai Elue:
As-machined: This is the raw finish achieved by machining a part. The surface will have visible machining marks, but for all parts machined in Shanghai Elue, we promise deburring as a standard regardless of the surface finishes you choose. As-machined finishes are usually very functional but not aesthetically pleasing. If not specified, surface roughness is 3.2μm as standard, and can be made to Ra1.6, Ra0.8, or even Ra 0.4μ depending on your exact applications.
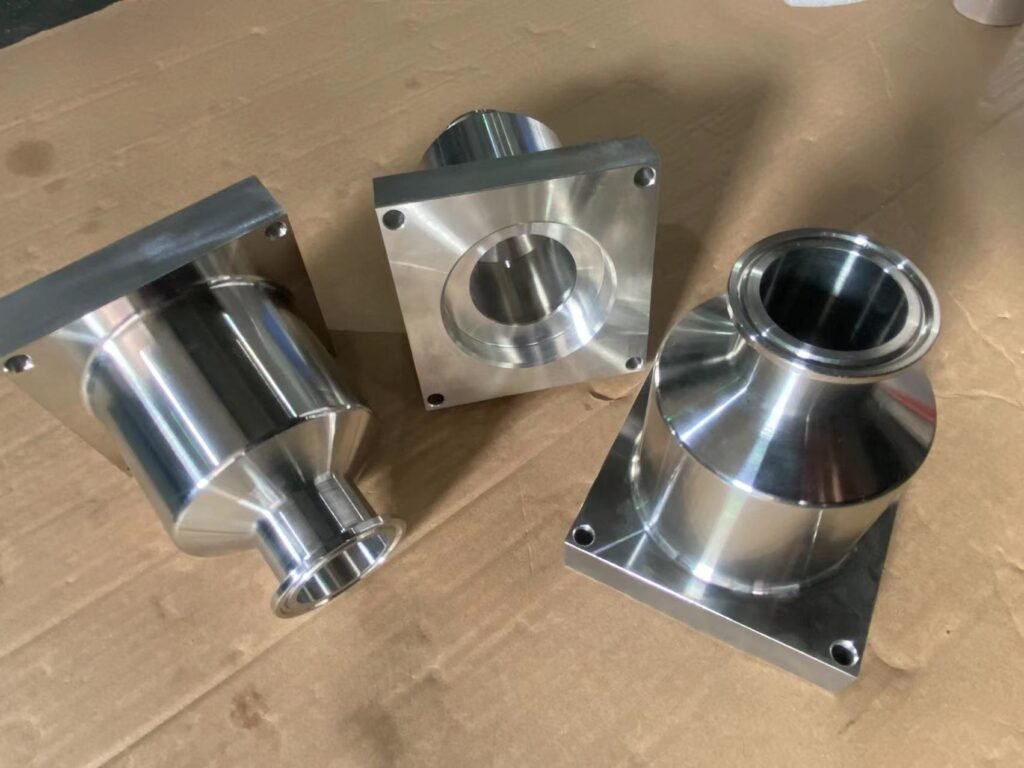
Bead blasting: This is a surface treatment process that uses pressurized air and small abrasive particles to create an even, matte finish on the part. Bead blasting is often used to create a non-reflective surface which can be beneficial when working with reflective parts. Our standard grit is #120 if not requested, and we have other available grits like #80, #100, and #150 depending on your special request.

Brushing: Brushing is a process that uses wire-bristled brushes to create an even, consistent finish on the part. This technique is often used for aesthetic purposes but can also be beneficial when working with parts that will have frequent contact with other surfaces because it helps reduce friction. Brushing grit available here is #400-600 and it can reach Ra1.6-1.2

Anodizing: Anodizing is a process that creates a protective layer on the surface of CNC machined parts made from aluminum or other metals such as titanium and magnesium. This oxide layer provides increased corrosion and wear resistance, as well as improved aesthetics. Anodizing is a popular choice for parts that will be subject to outdoor conditions, as it has high durability and color retention.
Heat Treating: Heat treatment is a process in which parts are heated to a specific temperature and then cooled quickly. This process alters the microstructure of the material, resulting in increased strength and improved wear resistance. Heat treating is usually used for parts that will be subjected to high temperatures or loads.
Painting: This type of surface finish is used when aesthetics are the main concern. Painting CNC machined parts offers additional protection against corrosion and wear, while providing a wide array of colors and textures, making them a great choice for parts that need to be attractive.
Powder coating: Powder coating is a popular choice for CNC machined parts that will be used outdoors, as it offers superior protection from corrosion and wears. It also provides an attractive finish that can be customized with a wide range of colors and textures.
Plating: Plating is a process of depositing a thin layer of metal on the surface of CNC machined parts, and there are many types of plating like zinc plating, nickel plating, copper plating, chrome plating, etc. This offers increased resistance to corrosion and wear, as well as improved aesthetics. Plating is often used on parts that will be exposed to harsh conditions, such as automotive engine components.
Tips on Choosing Right Surface Finish for CNC Machined Parts
When selecting the right surface finish for your CNC machining parts, consider the following factors:
- Application – Consider the environment that your part will be used in to determine whether it needs protection from corrosion or wear. Also, think about the aesthetic requirements of the part, such as if it needs to be painted or not. For example, parts that are used outdoors need to be protected from corrosion and wear, so a more resilient finish such as anodizing or powder coating is recommended.
- Materials – Different materials require different surface finishes in order to protect and preserve them. Consider the material that your part is made from and choose a finish accordingly. For example, aluminum parts can be anodized, bead-blasted, or painted while steel parts can be plated or powder coated.
- Cost – Generally, more complex surface finishes are more expensive than simpler ones. Consider your budget and the cost of the different finishes before making a decision.
It’s important to understand the requirements of your project and choose a finish accordingly. The right surface finish for CNC machined parts will depend on the specific application and requirements of each project. Once you have these factors in mind, you can look at the available surface finish options and make an informed decision.
Or If you need help selecting the right surface finish for your CNC machined parts, contact a professional machining company and they will be able to advise you.
Understanding Surface Roughness
If you have been working in a machining line for some months, below are some abbreviations you must be very familiar with, and these are all different ways to measure surface roughness.
Ra, Ra(arithmetic average) is the most commonly used method of measuring surface roughness. The Ra, also known as the Arithmetic Average (AA), is calculated by taking the arithmetic average of the absolute values of all the peak and valley points within a given sampling length. Ra is the most commonly used measurement for surface finish, as it provides a good indication of surface roughness. Ra is best suited for parts that need a relatively flat surface and doesn’t require any additional protection.
Rz, Rz is the average of the five highest peaks and the five deepest valleys within a given sampling length. Rz is best suited for parts that need to be smooth and flat, but also require a certain level of protection. Rz is typically used for parts that will be exposed to harsh conditions or environments where corrosion or wear is a concern.
RMS, RMS(root-mean-square) is the root mean square of all peak and valley points within a given sampling length. It’s calculated by taking the average of the squares of all peak and valley points. RMS is best suited for parts that need to be highly accurate and smooth, such as medical implants and precision instruments. This type of finish offers the highest level of protection against wear and corrosion.
Generally speaking, we typically measure surface roughness in micrometers or microinches — the smaller the measurement, the better the surface finish. For example, Ra0.4 should be a better finish than Ra0.8. Check the below article to learn more about surface roughness:
How to Reduce the Surface Roughness of the Workpiece
Conclusion
Choosing the right surface finish for CNC machined parts is important for ensuring that they are able to perform to their maximum potential. Consider the application, materials, and cost of the project when selecting a finish. Understanding the different types of surface roughness measurements can also help you select the best finish for your project. If you are unsure, contact a professional machining company to help guide you in making the best decision.