What is Titanium Machining
Titanium machining is a process of cutting titanium metal into different shapes and sizes. This process is important in the manufacturing industry because titanium is a strong, durable and lightweight metal that is increasingly being used in a variety of industries. Titanium machining can be done using different methods, such as milling, lathing, and drilling, however, Titanium machining is a complex process that requires special skills and knowledge.
Grades of Titanium We Work With
– Titanium Grade 2
Titanium Grade 2 is an extremely strong and lightweight titanium alloy that is widely used in many industries. Its high strength-to-weight ratio makes it an ideal choice for titanium machining applications. It is also highly resistant to corrosion and can withstand extreme temperatures, making it an ideal choice for aerospace and medical applications. Titanium Grade 2 is also easy to weld and fabricate, making it a versatile choice for many industries.
– Titanium Grade 5
Titanium Grade 5 is one of the most widely used titanium alloys. It is recognized for its high strength and toughness, high resistance to corrosion and ability to withstand extreme temperatures make it an ideal choice for aircraft and spacecraft applications where high temperatures are involved.
Different Types of Machines Used for Titanium Machining
There are various types of machining processes that can be used for titanium. The most common type of machining process is turning, which is where the titanium workpiece is held in a lathe and Cut with a cutting tool. Other common types of machining processes include milling, drilling, and EDM (electrical discharge machining). Each type of machining process has its own advantages and disadvantages. For example, turning is well-suited for creating cylindrical parts, but it is not as effective for making flat parts. As a result, it is important to select the right type of machining process for the specific task at hand. With the help of a skilled machinist, it is possible to create high-quality titanium parts using any of the aforementioned machining processes.

Benefits of Titanium Machining
Titanium is widely praised for its strength, durability and resistance to corrosion.
Titanium products are highly resistant to wear and tear, meaning that they will last longer and perform better than products made from other materials. In addition, titanium is an environmentally friendly material that can be recycled or reused, making it an ideal choice for sustainable manufacturing. Ultimately, the decision to use titanium machining should be based on a careful analysis of the benefits and costs. For many manufacturers, the benefits far outweigh the costs, making titanium machining an essential part of their operations.
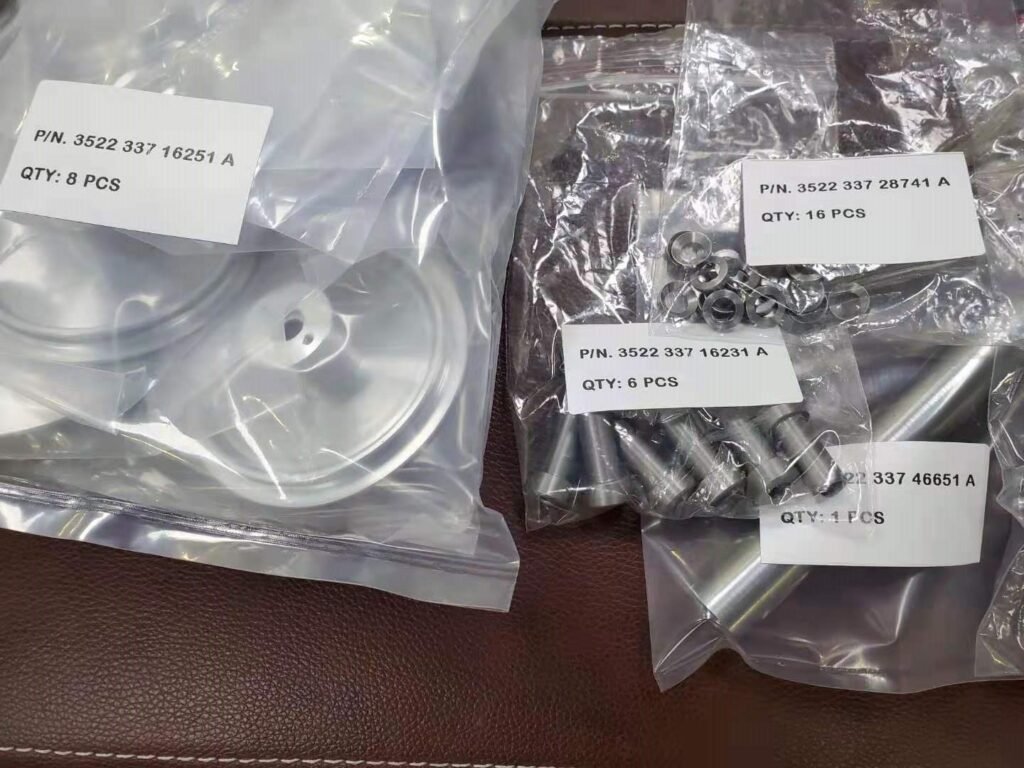
Challenges Associated With Titanium Machining
Titanium is a strong, lightweight metal that is frequently used in the aerospace and medical industries. However, it can be difficult to machine due to its high hardness and corrosion resistance. As a result, titanium machining often requires special tools and techniques. One common challenge is chip control. Because titanium is so hard, it tends to produce large, brittle chips that can quickly damage cutting tools. Another challenge is workpiece distortion. Titanium has a relatively high expansion rate, which means that it can distort significantly during machining. This can lead to poor dimensional accuracy and surface finish. Despite these challenges, titanium machining can be highly rewarding thanks to the unique properties of the metal. When machined correctly, titanium components are incredibly strong and resistant to wear and tear.
Finishes and Post-processing
There are a number of different titanium machining finishes and post-processing options available, depending on the desired final result.
– Anodizing, which creates a protective layer on the titanium surface. This can help to improve durability and resistance to wear and tear.
– Powder coating, which can give titanium a unique color or finish.
– Other options include polishing, sandblasting, and titanium plating. The type of finish and post-processing used will depend on the intended use of the titanium component. For example, components that will be exposed to high levels of wear and tear may require a more durable finish, such as anodizing or powder coating. Components that will be visible to the naked eye may require a finishing method that results in a more visually appealing finish, such as polishing or titanium plating.