Titanium is a strong, lightweight metal that is increasingly popular in machining. It has many uses in manufacturing and construction, and it is becoming very common in consumer products as well. Here we will provide a comprehensive guide to titanium machining, from the basics of the process to more advanced techniques. We will also discuss the many applications of titanium and how to get the most out of this versatile material.
What is Titanium Machining
Titanium machining is the process of cutting and shaping titanium using high-speed cutting tools. This process is used to create precision parts for all sorts of applications, from automotive and aerospace components to medical implants and consumer products.
The Properties of Titanium: As a material, titanium has an excellent strength-to-weight ratio and corrosion-resistant properties. It is also highly heat-resistant, making it an ideal material for parts that need to withstand high temperatures and pressure.
Types of Titanium Machining: There are several different types of titanium machining, including milling, turning, drilling, grinding, and EDM (electrical discharge machining). Each type of machining has its own benefits and drawbacks, so it’s important to choose the right method for your project.
The Applications of Titanium Machined Parts
Titanium machined parts are used in a wide variety of industries, including aerospace and automotive, medical, consumer products, sporting goods, military and defense, and more. The strength and lightness of titanium make it ideal for precision components that need to be strong yet lightweight.
Titanium is the most commonly used material for medical devices today. This is because it has excellent mechanical properties, such as strength, hardness, and ductility.
Custom-Made Medical Titanium Components:
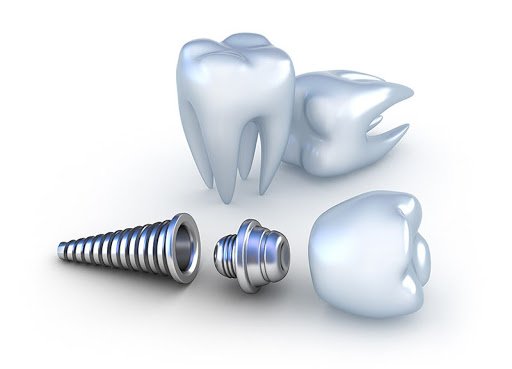
# Dental implant screws
# Orthopedic implants
# Artificial joints
# Bone fixation plates
# Clamps, cutters, and forceps
# Bone screws that are tapered, straight, or self-tapping
# Tunnellers and Dilators
Aerospace Components Application for Titanium Machining:
The main thing that makes aerospace components different from other kinds of parts is that they must be strong enough to hold up under extreme conditions. Titanium is used to make aerospace components because it’s lightweight and strong enough.

Some of the titanium parts used in aerospace engineering include:
• Fasteners and bolts
• Injection manifolds
• Fuel lines
• Landing gear components
• Structural supports
• Rotor blades
Titanium Machining Parts used for Automotive Industry:
The automotive industry relies heavily on titanium parts due to its light weight and strength. It is used in the production of various components including:
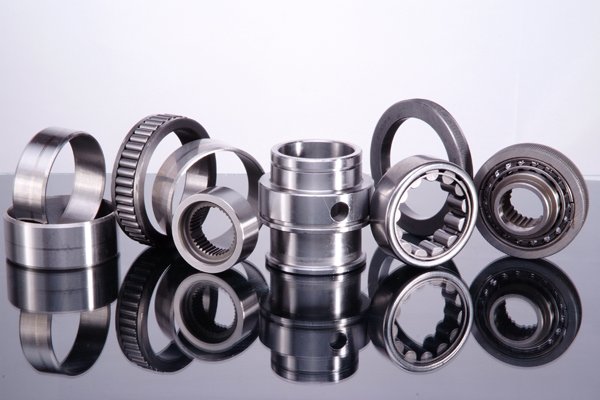
• Exhaust systems
• Engine components
• Brake calipers
• Pistons
• Suspension systems
• Wheel rims
Defense Applications of Titanium Machining:
Titanium is an ideal material for components used in military and defense applications due to its strength, corrosion resistance, and heat resistance.
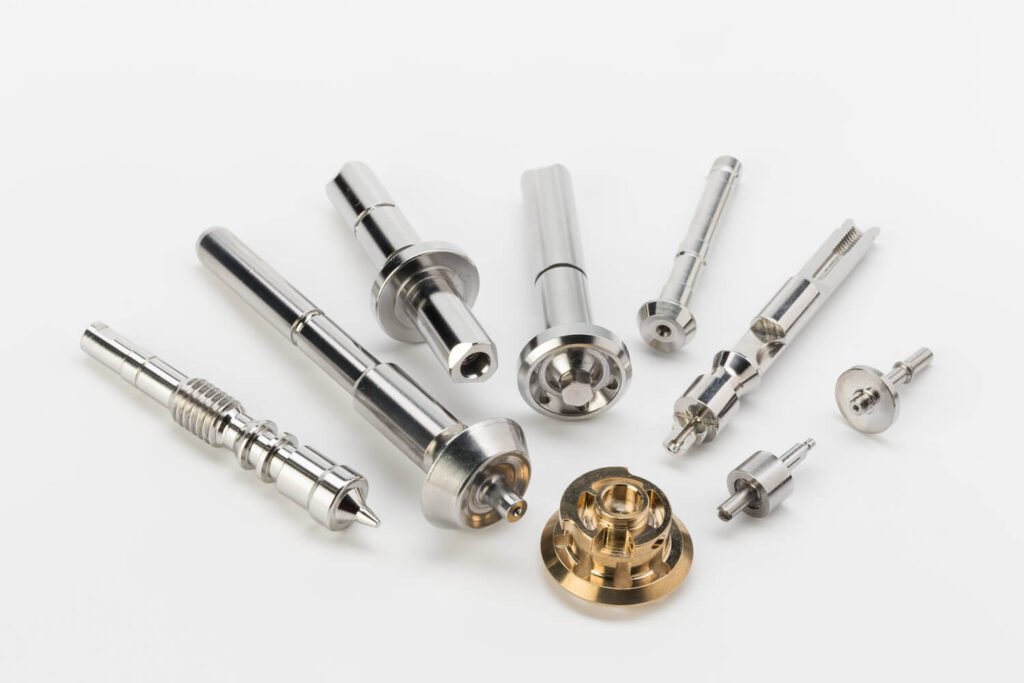
Some of the titanium parts used in defense engineering include:
• Aircraft armor
• Weapon systems
• Naval vessels
• Radar arrays
• Missile cas
The Different Types of Titanium Alloys That Can be Machined
Titanium alloys are a combination of titanium and other metals, and there are more than 100 kinds, each alloy has its own characteristics and benefits.The most common titanium alloys used in machining are Ti-6Al-4V (6% aluminum, 4% vanadium), Ti-5Al-2.5Sn (5% aluminum, 2.5% tin), and TI-2AL-1.5Mn (2% aluminum, 1.5% manganese).
These titanium alloys are popular because they combine the strength of titanium with the corrosion-resistant properties of other metals. They can also be machined more easily than pure titanium, making them a great choice for complex parts.
According to their effects on transformation temperature, titanium alloy elements can be divided into three types: α alloys, (α+β) alloys and β alloys.
α alloys have got stable structure, and it’s more wear-resistant than pure titanium whether in normal or high temperature, but they can’t be heat treated.
(α+β) alloys are stronger than α alloys, but still relatively easy to machine, and they have good comprehensive performance due to their mixture of α and β structures. It’s suitable for complex parts with complex shapes.
β alloys are the strongest titanium alloys and are extremely difficult to machine. They are also called an age-hardenable alloy, it has excellent welding properties as well as high-temperature strength and toughness. They are often used in applications where strength is paramount, such as aircraft and aerospace parts.
The Advantages and Disadvantages of Titanium Machining
The advantages of titanium machining are that it is strong, corrosion-resistant, and light weight. This makes it ideal for components used in aerospace and defense applications. Additionally, titanium alloys can be machined more easily than pure titanium, making them a great choice for complex parts.
Resistance to corrosion: Titanium is highly resistant to corrosion and oxidation in wet or moist environments, making it ideal for components exposed to saltwater or other corrosive elements.
High heat tolerance: Titanium has a high melting point, which makes it suitable for applications that involve extreme temperatures.
Biocompatible: Titanium is biocompatible, making it well-suited for medical implants and devices.
Low thermal expansion: Titanium has a low coefficient of thermal expansion, meaning that it does not expand or contract significantly in response to temperature changes. This makes it ideal for parts that require tight tolerances.
Strength: One of the biggest advantages of titanium is its strength over other materials. Titanium is extremely strong for its weight, making it a good choice for lightweight components.
The main disadvantage of titanium machining is that it can be difficult to machine due to the high temperatures and pressures needed to cut it effectively. This means that cutting tools must be able to withstand these conditions without breaking or wearing down quickly.
Additionally, titanium is a more expensive material than other metals and alloys, making it costlier to produce parts from. Finally, titanium is not magnetic and does not conduct electricity, making it unsuitable for certain applications.
Common Challenges Associated With Titanium Machining
Evan titanium is a great material to use in many extreme applications, it does present some unique challenges. Below are some challenges associated in titanium machining:
1. Excessive tool wear: Due to its strength and hardness, titanium is prone to accelerated tool wear. This means that the cutting tools will need to be replaced more frequently than when machining other materials.
2. Compromised surface finish: When titanium is machined, it can produce a poor surface finish if the correct parameters and tooling are not used. This can result in components with rough edges or unwanted burrs.
3. Difficult to machine: Titanium is a difficult material to machine due to its strength, hardness, and tendency to heat up quickly. This means that special cutting tools must be used and high-pressure coolants may also be needed.
4. Low tolerance for machining errors: As titanium is difficult to machine, any errors can quickly become costly and time-consuming to fix. Additionally, the high cost of titanium makes machining mistakes very expensive.
Overall, the advantages of titanium machining outweigh its disadvantages when it comes to producing components with superior strength and corrosion resistance.
Tips to Improve Titanium Machining
1. Use sharp cutting tools: Sharp cutting tools are essential for machining titanium and other tough materials successfully, as they reduce the pressure on the tooling while ensuring a clean cut.
2. Utilize high-speed machining techniques: High-speed machining is usually used when machining titanium to minimize wear on the cutting tools. This involves using higher feed rates and spindle speeds than usual, as well as shorter cuts when possible.
3. Use appropriate coolants: Coolants are used to keep the cutting edge from overheating during machining operations. When machining titanium, it is important to use an appropriate coolant that is designed for high-speed machining and will not break down easily.
4. Regularly replace coolants: Coolants should be changed regularly to ensure that the cutting edge remains sharp and that excessive tool wear is avoided.
5. Use correct clamping techniques: Proper clamping of the workpiece is essential for successful titanium machining, as it will help to keep the tool from deflecting and ensure that it cuts accurately.
6. Ensure correct cutting parameters: The correct cutting parameters must be used when machining titanium, as this will help to reduce wear on the tooling and ensure a good surface finish.
By following these tips, manufacturers can improve their efficiency and accuracy when machining titanium components. Additionally, these tips can help to reduce the risk of tooling failure and increase productivity in the long-term.
Conclusion
Titanium machining can be a challenging process due to its hardness and strength, however the rewards far outweigh the difficulty when it comes to producing components with superior properties. By taking into consideration the unique challenges associated with titanium machining, as well as following proper cutting techniques and parameters, manufacturers can ensure that their parts are produced efficiently and accurately.
Shanghai Elue is an experienced machining supplier and has many years of experience in titanium machining. We have the latest CNC machine tools and experienced staff to ensure high-quality parts are produced every time. Contact us today for more information on our titanium machining services.
FAQs about Titanium Machined Parts:
Q: Why is Titanium Difficult to Machine?
A: Titanium is a strong and durable metal, but it’s also quite difficult to machine. This is because of its strength; when machining titanium, cutting tools must be able to withstand high temperatures and pressures without breaking or wearing down. Additionally, titanium has a low thermal conductivity, meaning that heat builds up quickly in the tooling and the workpiece, making it difficult to keep the cutting edge cool.
To machine titanium effectively and reduce wear on tools, high-speed machining is often used with sharp cutters and appropriate cutting fluids. Additionally, titanium alloys can be machined more easily than pure titanium due to their combination of strength and corrosion resistance. Finally, coolants should be regularly changed to ensure the cutting edge stays sharp and that excessive wear is avoided.
Q: What Are the Benefits of Titanium Machined Parts?
A: Titanium machined parts offer a number of benefits over other materials. These include excellent strength-to-weight ratio, high corrosion resistance, and excellent thermal and electrical conductivity. Additionally, titanium is biocompatible, making it an ideal choice for medical implants.
Q: What do you need to machine titanium parts?
A: Machining titanium requires specialized tools, as well as high feed rates and spindle speeds. Additionally, coolants should be used to keep the tooling from overheating, and the workpiece needs to be properly clamped in order to ensure accuracy. Finally, correct cutting parameters should be applied in order to reduce tool wear and ensure a good surface finish.
Q: Can titanium be welded?
A: Yes, titanium can be welded using the appropriate welding processes and equipment. However, due to its strength and low thermal conductivity, welding titanium is more complex than other metals and should only be done by experienced professionals. Additionally, it’s important to use the correct filler materials and welding parameters in order to ensure a strong joint and minimize warping.
Q: What is the cost of titanium machining?
A: The cost of titanium machining depends on factors such as the complexity of the part, quantity needed, and time frame required. Generally speaking, machining titanium components is more expensive than machining other metals due to the specialized tools and techniques required. Additionally, high-speed machining processes may also be needed in order to produce parts efficiently and accurately.
Q: What is the easiest titanium to machine?
A: The easiest titanium to machine is 6AL-4V, which is an alloy made with titanium, aluminum and vanadium. This alloy offers good machinability due to its combination of strength and corrosion resistance. However, it’s important to note that other alloys may require different cutting parameters in order to achieve the desired results.
Q: What is the cutting speed for titanium?
A: The cutting speed for titanium is typically higher than other metals due to its strength and low thermal conductivity. Additionally, the feed rate should be adjusted according to the complexity of the part, as well as the tooling and coolant used. Generally speaking, it’s best to use lower speeds with sharp cutters in order to reduce wear on the tooling and ensure a good surface finish.
Q: What is the shear strength of titanium?
A: The shear strength of titanium depends on the alloy used. Generally speaking, 6AL-4V has a shear strength of 425MPa while Grade 5 (Ti6Al4V) has a shear strength of 880MPa. It’s important to note that other alloys may have different strengths, so it’s essential to always consult the material datasheets before machining.
Q: What are the most common titanium alloys for machining?
A: The most common titanium alloys for machining include Ti5 (Ti6Al4V), 6AL-4V, and Ti2. Each of these alloys offers different levels of strength and corrosion resistance, so it’s important to select the alloy that best suits the application. Additionally, specialized tooling may be required in order to properly machine certain alloys.
Q: What coating is best for titanium machined parts?
A: The best coating for titanium machined parts depends on the application. Generally speaking, hard anodizing is a popular choice, as it provides excellent wear resistance and corrosion protection while also preserving the part’s dimensional accuracy. Additionally, nickel plating and TiN (titanium nitride) coatings can be used to improve hardness, reduce friction, and enhance wear resistance. It’s important to always consult the material datasheet in order to determine the best coating for any given application.
Q: How to Choose the Right Tool for Milling Titanium?
A: When selecting a tool for milling titanium, it’s important to consider the complexity of the part, as well as the speed and feed rate needed. Generally speaking, titanium should be machined with high-speed steel or carbide tools in order to achieve optimal results. Additionally, sharp cutters with low cutting speeds are recommended in order to minimize wear on the tooling and produce a good surface finish.
Q: Does titanium easily warp when machining?
A: Titanium can warp when machining due to its low thermal conductivity. To reduce the risk of warping, it’s important to use coolants and cutting parameters that prevent excessive heat buildup in the workpiece. Additionally, careful consideration should be taken when selecting joint designs and clamping
Q: Is titanium difficult to machine?
A: Titanium can be difficult to machine depending on the alloy used and the complexity of the part. Generally speaking, titanium machining requires specialized tools and techniques in order to achieve optimal results.
Q: Which is better, Grade 2 or Grade 5 Titanium?
A: Grade 5 (Ti6Al4V) titanium is generally considered to be the best alloy for machining due to its combination of strength and corrosion resistance. It also offers good formability, weldability, and high temperature performance. Grade 2 titanium is less expensive but has lower strength and inferior corrosion resistance compared to Grade 5. Ultimately, the best grade to use will depend on the application. It’s important to always consult the material datasheet in order to determine which alloy is best for any given situation.