What is WEDM?
Slow wire EDM is a type of machining which uses continuous moving metal wire (called electrode wire) as electrodes to remove metal and cut and shape the workpiece by pulse spark discharge. The principle of slow-wire machining is that there is a gap between the electrode and the workpiece, and the metal is removed by continuous electrical discharge.
There are fast wire cutting and slow wire cutting from the cutting speed, generally speaking the workpieces processed by fast wire is usually in the range of Ra = 1.25 ~ 2.5 μm, and the slow one can reach up to Ra = 0. 16μm. Besides,the fixed tolerence, linear tolerence and size tolerence of slow wire cutting machines are better than the fast wire and it will also provide a very smooth surface finish that requires no secondary grinding.
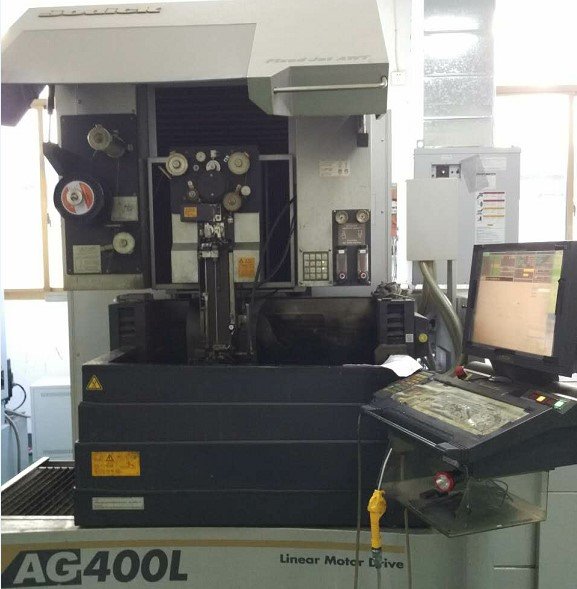
Applications of Wire EDM
Slow wire cutting is widely used in many industries like aerospace, electronics, telecommunications, and the molds making like stamping die, plastic molds, Powder metallurgy molds. Among them, the punching die, punching fixing plates, stripper plates and other precision holes processing. And about the injection molds, the common application includes the mold insert holes, the thimble holes, the lifter holes, and the slides processing, and the precision required is not so high as the stamping molds.
Advantages of WEDM
1. machining efficiency improvement
At present, the high efficiency of the advanced slow wire-cutting machine can reach 500 mm 2/min. and the machining efficiency of the thick workpieces has significant technical improvement, for example,when cutting 300 mm thick workpieces, it can reach 170 mm 2/min. For the machining of the variable thickness workpieces, the higher processing efficiency can be achieved by automatically detecting the thickness of the workpiece and automatically adjusting the processing parameters to prevent wire break.
In addition, the fast automatic wire threading technology introduced by the advanced slow wire cutting machine, the automatic wire threading time can be done at < 15s, which highly improves the efficiency of the processing operation. And when the double wire automatic exchange technology is introduced, the electrode wire of 0.20 ~ 0.02 mm can be used for automatic double-wire switching processing. The thick wire is used for the previous cutting, generally the diameter of the wire is 0.25 mm to improve the processing efficiency, and can be cut without core; then the fine wire is used for finishing, generally the 0.10 mm fine wire is used to cut the small round corner, and the precision can be improved, overall, 30% ~ 50% cutting time can be saved.
2. machining accuracy improvement
Multi-cutting technology is a good way to improve the machining accuracy and surface quality of the slow-wire cutting. First step is to cut a shape, secondary cutting is to improve accuracy, and finally is to improve the surface quality.
The corner will collapse due to the lag of the electrode wire when cutting it. In order to improve the corner cutting accuracy, more dynamic corner processing strategies are adopted. Such as: automatic change of processing speed, automatic regulation of water pressure, control of processing energy.
The high-precision machining loop adopted by advanced slow-wire machine is an effective technology to improve the straightness of workpieces, and the precision of thick workpieces is greatly improved. In order to carry out micro-precision machining of small fillet, narrow slot, narrow slot and fine parts, high quality NC low-speed wire electrical discharge machining (WEDM) machine tool can use 0.02 ~ 0.03 mm electrode wire to cut.
3. surface quality improvement
The advanced slow wire cutting machine adopts the non-protective electrolytic pulse power supply with the average voltage of zero, the electrolytic damage has been reduced to a lower degree. In addition, due to the improvement of pulse power supply, high peak value and narrow pulse width (microsecond level) are generally used. Most materials are thrown out in gas phase, which takes away a lot of heat. The surface temperature of the workpiece can not go up and the phenomenon of cracking is greatly reduced, so it greatly improves the surface quality. The surface metamorphic layer can be controlled below 2μm by using non-electrolytic power supply in wedm. Besides,the wear resistance of the cutting edge for the hard alloy punch dies is almost same as the grinding surface, even better than the mechanical ground finish. Right now more and more precision machine parts are“To cut instead of grinding.”
Shanghai Elue WEDM Service
Right now we have 10sets of Sodick WEDM machines in-house,which were imported from Japan directly.
Since 2006,Shanghai Elue has been providing high precision machining solutions for top-end market. And we’re an ISO- and IATF-certified machine shop with the in-house capabilities to carry out a wide range of EDM machining projects,which we’re confident will exceed your expectations.
In recent years, we have invested quite a lot on machine operators, advanced equipment and technology, which helps our customers gain competitive edges in today’s challenging global marketplace.
In conclusion, wire EDM can be used to machine any conductive materials,and this type of work is typically low volume, made from hardened materials, and requires very high precision.
For additional information about our precision wire electrical discharge machining capabilities, please refer to the specification table below or contact us directly by email sales@imachinepart.com