CNC machining technology has been remarkably evolved over the years and is considered the backbone for many major industries, but during the machining process the problem of workpiece deformation is still a big headache.
There are many factors that control the actual shape of the workpiece in CNC machining, but if the final product exceeds the permissible error range and there are differences between the CAD design and workpiece manufacturing, then the workpiece will be scrapped.
Overview of Workpiece Deformation in CNC Machining
Workpiece deformation in CNC machining occurs when the motion of cutting tools, fixtures, and spindles creates uneven pressure on the workpiece, resulting in skewed or distorted shapes. This type of distortion can be caused by a variety of factors including incorrect tooling setup, inadequate material properties, and poor maintenance. It is important to understand the causes of workpiece deformation in order to minimize and correct it.
Workpiece deformation can have a significant effect on the accuracy and quality of machined parts. Distortion of the workpiece can cause out-of-tolerance dimensions, surface finish problems, reduced strength, and even failure of components in extreme cases. It is important to identify and address any sources of deformation in order to produce parts with the required level of accuracy and reliability.

To solve the deformation problems, firstly we have to understand the manufacturing process and the deformation mechanism.
Causes of Workpieces Deformation in CNC Machining
In order to get a perfectly designed workpiece, we need to minimize the risk prospect and degree of deformation as much as possible throughout the machining process. Below we elaborated the causes of workpiece deformation and proposed practically implemented preventive measures to tackle with this issue.
1: Workpiece Material and Structure
The workpiece deformation is directly proportional to the complexity in the shape, length to width ratio, wall thickness of the blank, and rigidity and stability of the material. While designing the specific part, it is made sure that the impact of above-mentioned factors should be as minimum as possible on the workpiece to avoid deformation.
2: Workpiece Clamping
To avoid deformation during clamping, the clamping point should be selected carefully and the clamping force must be pertinent as per the position of the clamping point. Thus, try to keep the clamping point and supporting point of the slack as consistent as possible and let the clamping force be exerted on the support in order to keep the clamping point closer to the machining surface. In this way, workpiece deformation caused by the clamping can be largely avoided.
When more than one clamping force is acting on the workpiece from various directions then the order of the forces is very important. The clamping forces of the workpiece and the support must be exerted first and the main clamping force of the balanced cutting forces must act lastly.
Adopting the above-mentioned precautions regarding workpiece clamping and the increase in the contact area between slack and fixture, and also the increase in the rigidity of the parts are very helpful in reducing workpiece deformation by clamping.
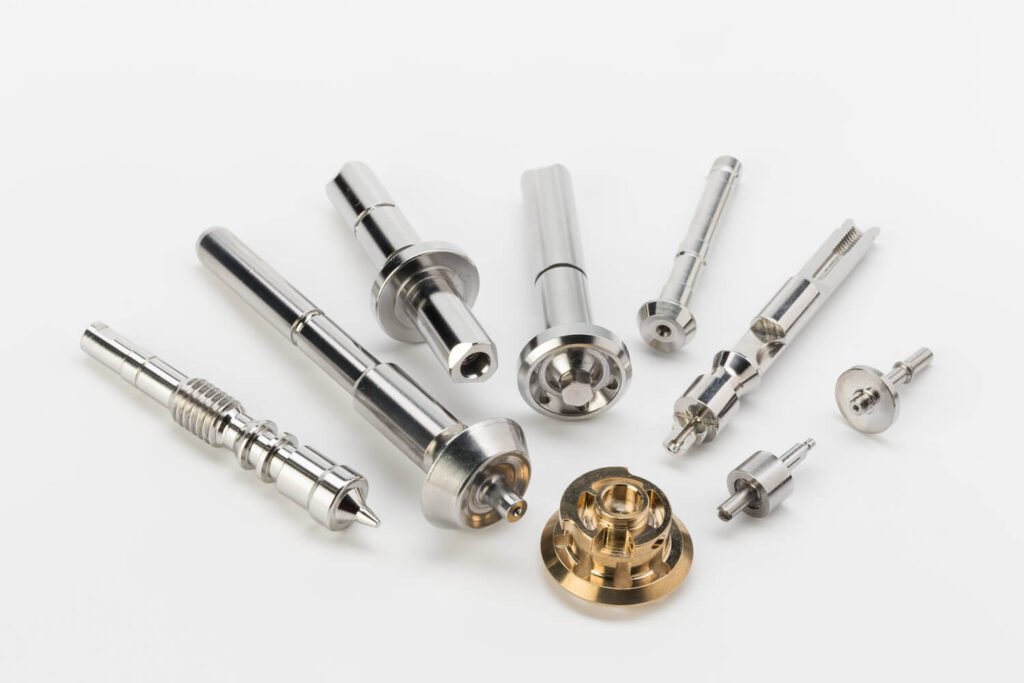
3: Residual Stress and Internal Stress
The internal stress caused by external forces plays a significant role in workpiece deformation. When we apply external force that interacts with the internal crystalline structure of the workpiece and produces internal stress into it. This internal stress causes slack’s internal structure to rebalance its original state.
We can get rid of internal stress and there are three methods to eliminate it:
- Heat Treatment of the Finished Workpiece
- Aging Treatment with External Vibration
- Aging Treatment in Natural Environment
After the application of the above-mentioned methods to eliminate internal stress, sometimes it does not get eliminated completely and there will remain a small quantity of residual stress that can cause the workpiece to deform.
Also, there are three methods to deal with residual stress:
- Implement Heat Treatment Process On Parts
- Optimize the Internal Structure Design of Parts
- Reasonably Arrange the Process Flow
4: Workpiece Cutting Tool
Workpiece can also be deformed if not processed properly. While cutting the workpiece, it could have elastic deformation because of the cutting forces and this elastic deformation occurs in the direction of force. This sort of deformation can be tackled by using a sharp cutting tool during workpiece processing and it minimizes the friction resistance between tool and slack. This in turns ameliorates the heat dissipation capacity of the cutting tool and helps in the reduction of residual internal stress on workpiece.
A comparison of numerous processing treatments on workpiece shows that the degree of deformation against each machining factor is found to be different, but the material, workpiece clamping and machining process have the greatest influence on slack deformation.
Now the question rises, how we can deal with this technical issue?
Measures to Prevent Workpiece Deformation in CNC Machining
There are several methods that can be used to minimize workpiece deformation in CNC machining operations. These include using proper tooling setup, selecting an appropriate cutting speed, using low-deformation materials, using correct fixturing, balancing cutting forces, and performing regular maintenance. By taking steps to reduce deformation risks and troubleshooting any problems that may arise, it is possible to ensure accurate and high-quality machined parts.
1: Selecting Appropriate Materials According to the Workpiece Structure Requirements
Poor material selection and unreasonable workpiece structure design will definitely lead towards deformation. Let’s first talk about the material selection for a workpiece.
For example, if we want to introduce sufficient hardness into the frame then we should use cast iron and if workpiece demands heavy-duty and volatility then alloy steel could be preferred. But if we require some specific material characteristics then we can use surface shot peening, quenching and other processing techniques. The appropriate material selection is very important because it affects workpiece use and its service life.
Other important factor causing workpiece deformation is its structure. If a proper workpiece structure design is selected then it can minimize deformation such as avoiding instant design changes in the structure during the CNC process, and please try to design a center-symmetric structure to avoid excessively long or thin workpiece structures.
If we continuously change the workpiece structure under the same material then the deformation in the final product is absolutely necessary. Therefore, while manufacturing the workpiece, try to make it as exact as possible so, you should not have to change it during the process.
2: Choosing an Appropriate Clamping Method
Workpiece clamping method also affects workpiece deformation and the poor selection of positioning surface causes deformation mainly. According to the principle of reference coincidence design, when selecting the positioning surface we must choose the workpiece area that has the largest contact surface to attain a thorough workpiece stability during CNC machining process. After the positioning surface is fixed, we start marking clamping point that correspond to the positioning support point one by one.
This workpiece clamping method assures an appropriate clamping force that cancels the clamping force and support force out while eliminating internal stress in the workpiece. While determining the clamping force,there are two factors to be considered, first is to make sure that the clamping is stable and dependable and second is to minimize workpiece deformation.
3: Reducing Workpiece Internal Stress
When the workpiece is being manufactured, it will unavoidably bear the squeezing force and the friction force that are the main reason of various internal stresses for the workpiece. To eliminate the effect of external forces, the symmetrical processing methods are normally used to balance the stress changes inside the workpiece during machining process.
To obtain thorough workpiece stability, opposite forces are being applied on two planes that are symmetric about a center. Before the start of the process, the workflow will be like this, firstly the slack roughing will be done then finishing processes are applied. While three elements of cutting are carefully exercised i.e., cutting speed, feed rate and cutting depth and numerous suitable cutting tools for roughing and finishing processes.
When manufacturing an asymmetrical structured workpiece then the blank processing can adopt anti-deformation means i.e., reserve the amount of deformation in the opposite direction of the deformation position of the workpiece.
4: Reducing the Effect of Cutting Force
Cutting force may also cause workpiece deformation if not properly applied. It is advisable to choose cutting tool accordingly and also the size of the cutting fore carefully. During CNC machining process, the manufacturing heat must be eliminated and the part should be cooled continuously in order to reduce thermal conductivity.
For different cutting stages of the slack, the differentiated cutting parameters should be selected accordingly such as during the rough machining stages, it is suitable to choose a larger cutting force and reduce the cutting feed to enhance cutting efficiency. And during workpiece finishing stages, the speed of knife must be reduced and cutting speed should be increased to achieve better surface processing quality.
Most of the heat during CNC machining process generates because of the friction between the tool and the workpiece. If appropriate cooling is not provided in time then it will surely deform the workpiece. One more thing, if applying high-speed cutting,it will surely decreases the processing time but reasonable cooling should be applied to avoid deformation.
Other Measures
The stress produced in the workpiece due to external forces should be released after finishing the machining process and here we can use some effective methods. Also, special protection fixtures, vibration aging, and correction methods can also be implemented. Like a vibration aging equipment is found to be very helpful in residual stress reduction inside the workpiece and better its fatigue strength.
Conclusion
Workpiece deformation can have a significant impact on the accuracy and quality of machined parts. It is important to understand the causes of workpiece deformation and take steps to reduce its risks. With proper tooling setup, selection of low-deformation materials, correct fixturing and balancing of cutting forces, it is possible to minimize and even eliminate workpiece deformation in CNC machining operations.